介绍了两种典型的喷丸强化方法(气动式喷丸和离心式喷丸),分别从应用范围、加工效率、喷射原理、表面完整性等方面对其进行了比较。为揭示喷丸强化机制,概述了喷丸工艺数值模拟与工艺参数优化方法,分析了喷丸对齿根表面完整性影响机制,并阐述了表面完整性参量之间的相互作用关系。同时,阐明了齿轮喷丸后的疲劳断裂机理,包括裂纹萌生与扩展机制。在此基础上,重点论述了受喷齿轮弯曲疲劳性能的影响因素,并提出了改善齿轮疲劳强度的措施。此外,简要探讨了齿轮喷丸后,疲劳强度提升幅度问题,并归纳了受喷齿轮弯曲疲劳建模方法。最后,对齿轮齿根喷丸强化工艺进行总结,并对其发展趋势进行了展望。
齿轮是机械传动的核心零部件,以汽车齿轮为例,根据功能不同可分为变速箱齿轮、差速器齿轮、车桥齿轮、发动机齿轮等。目前国内常见汽车齿轮钢有 20CrMnTi、22CrMoH、20CrNiMo、20CrMnMoH 等,而国外常见汽车齿轮钢主要包括 SAE 4320(美国)、SCr420H(日本)、EN35(英国)、20MnCr5(德国)等。齿轮运行过程中常出现弯曲疲劳与接触疲劳失效,严重影响了齿轮服役寿命。弯曲疲劳失效是交变载荷作用下齿根弯曲应力所致。齿轮在工作时常被视为一支悬臂梁,齿根相当于悬臂梁的支点,齿根圆角处为最大弯曲应力集中区域,疲劳裂纹从此处萌生,若所受载荷较高,且拉应力较大,齿轮会出现早期失效。在齿轮啮合过程中,受载一侧齿根圆角半径处产生拉应力,而在另一侧齿根圆角半径处受到压应力。经过多次循环后,在齿根受拉程度最高处,易出现疲劳裂纹,而当齿根承受压应力时,则不易出现疲劳裂纹。
在交变载荷条件下,齿轮弯曲疲劳失效分为三个阶段:第一阶段,微裂纹在齿根圆角处萌生;第二阶段,裂纹扩展到齿轮内部;第三阶段,裂纹迅速延伸扩张,齿轮断裂,齿根弯曲疲劳失效,如图 1 所示。接触疲劳是齿轮接触区赫兹接触应力与剪切应力共同作用引起的,其失效形式以点蚀与剥落为主。随着近几年汽车行业的高速发展, 轻量化、高承载以及长寿命等高性能齿轮的需求量日益增加,这对齿轮抗疲劳性能提出了更高的要求,因而齿轮表面强化技术显得尤为重要。
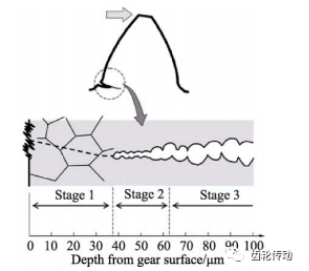
图 1 齿轮齿根弯曲疲劳失效示意图
目前大多数汽车齿轮都是采用渗碳、淬火工艺进行表面硬化,可在一定程度上提高齿轮疲劳强度。但齿轮表层残余压应力水平较低,疲劳性能提升水平有限,因而只能满足一般齿轮使用性能要求。喷丸强化技术是一种金属表面冷加工技术,其工作原理是高硬度、高速运动的弹丸冲击工件表面,在工件表层引入残余压应力。如图 2 所示,喷丸诱导残余压应力抵消了工件外部载荷,从而提高工件抗疲劳性能。喷丸工艺通常与渗碳、淬火等热处理工艺复合对齿轮进行表面强化,齿轮喷丸后的承载能力可提升 20%~30%。在不需增加齿轮尺寸与重量的情况下,设计人员可通过喷丸提升齿轮承载能力与疲劳强度,并达到节约生产成本的目的。
此外,喷丸的优势还表现在:1)喷丸诱导残余压应力层可防止齿面裂纹与点蚀;2)喷丸引入的弹坑有储油功能,可提高齿轮润滑性能,防止齿轮胶合、磨损、剥落发生,以及降低齿轮工作温度;3)喷丸可消除齿轮机械加工留下的刀痕,减少齿轮表面应力集中;4)喷丸可减少渗碳表层异常组织等。因此,喷丸作为一种提高齿轮疲劳强度、承载能力,并满足齿轮轻量化设计要求的表面强化工艺,被广泛应用于齿轮制造领域。
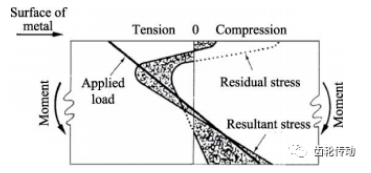
图 2 外载荷下工件残余应力
目前,围绕渗碳齿轮喷丸强化工艺,在工程实践中,齿根疲劳性能的关注度普遍高于齿面,而且关于齿根喷丸强化的研究报道较多。为促进喷丸强化工艺在渗碳齿轮齿根抗疲劳方面的应用,本文介绍了两种典型的喷丸强化工艺(气动式喷丸和离心式喷丸),列举了其各自特点,并在此基础上指出了齿轮喷丸工艺选取原则。首先,分析了喷丸工艺数值模拟与工艺参数优化方法,阐述了喷丸对齿根表面完整性(残余应力、硬度、粗糙度、微观组织)的作用机制,并探讨了表面完整性参量之间的相互作用关系,从而揭示了喷丸强化机理。其次,对喷丸处理齿轮疲劳断裂机理进行了综述,重点总结了渗碳齿轮喷丸处理后,影响弯曲疲劳性能的因素,并提出了弯曲疲劳性能改善措施。此外,探讨了齿轮喷丸后,弯曲疲劳性能提升幅度问题,并归纳了齿轮喷丸强化后,弯曲疲劳性能建模方法。最后,对齿轮齿根喷丸进行了总结,并对其发展趋势进行了展望,以期对齿轮喷丸强化工艺的理论研究与实践应用提供一些参考。在没有特殊说明的情况下,文中的渗碳代表普通渗碳热处理。
1 喷丸强化工艺方法
喷丸强化工艺通常包括气动式喷丸(Air-blast peening)与离心式喷丸(Centrifugal peening),其中离心式喷丸又称为抛丸。两者均属于机械喷丸工艺,最大差异在于喷射动力和方式。气动式喷丸是利用压缩空气驱动丸粒冲击工件表面;而离心式喷丸工艺是利用叶轮高速旋转,通过离心力作用将丸粒抛向工件表面。两者目的均是在工件表面产生残余压应力,起到表面强化作用,这与喷砂的用途(工件表面除锈、去除氧化皮)不同。气动式喷丸与离心式喷丸各有特点,表 1 从喷射方式、丸粒特性、应用范围、效率等方面,对两种不同的齿轮喷丸方式进行了对比。由表 1 可见,两种齿轮喷丸方式并没有绝对的优劣之分。离心式喷丸方法加工效率高,对大模数齿轮加工优势突出,但对齿轮外形依赖性大,复杂外形齿轮难以达到均匀覆盖率;气动式喷丸可精确控制喷射位置,但加工效率低。因而,选择喷丸工艺方法时,需根据产能、成本、齿轮外形和尺寸综合考虑。为集成两者的优势,喷-抛丸混合喷丸系统将成为发展趋势。另外,通过文献分析可知,相同喷丸工艺参数(弹丸参数、材料参数、设备参数)下,采用上述两种加工方式所加工齿轮的使用性能之间的对比研究较少。表 1 显示,相同喷丸工艺参数下,分别采用两种不同的喷丸工艺所得到的喷丸效果差异明显。因此,工程实践中,采用不同喷丸方法欲达到满意的齿轮喷丸效果,需依据抛喷丸标准,分别设计不同的喷丸工艺参数(例如喷丸强度)。
表 1 喷丸强化方法比较
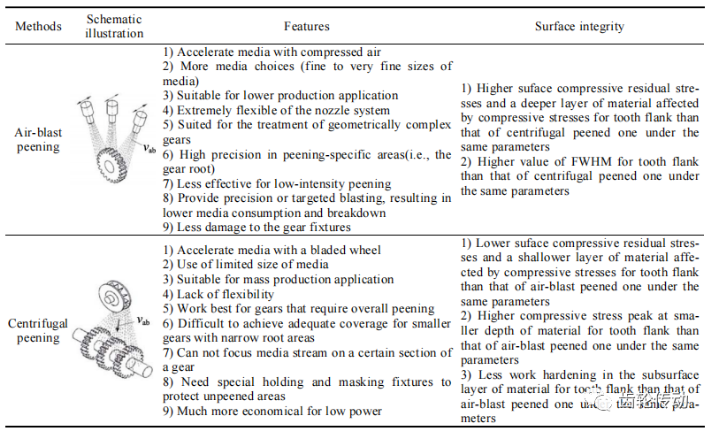
2 喷丸强化数值计算
数值模拟技术为深入揭示喷丸机理提供了强有力支持,可以降低试验成本,缩短研发周期。喷丸工艺仿真是关于几何与物理非线性的初值与边界值求解问题。Comandini 等忽略渗碳引入的残余压应力,对 Ni-Cr 渗碳直齿轮喷丸后齿根分别进行了二维与三维残余应力场数值模拟,仿真模型如图 3 所示。
结果表明,残余压应力峰值仿真结果与试验结果之间的误差小于 7%,齿根外表面试验值大于仿真值。针对齿轮喷丸强化工艺过程中,齿顶边缘容易出现翻边,进而影响齿轮啮合性能,Garijo 等基于 Workbench 有限元分析软件,提出了一种渗碳直齿圆柱齿轮喷丸后翻边预测与分析方法,研究表明,喷丸速度、喷嘴相对于齿轮的位置对翻边的形成影响最大;弹丸流从齿顶向有效齿廓喷射产生的变形量最大,高速弹丸冲击齿廓边缘的最大变形量可达 0.024 mm。考虑齿轮渗碳引入的残余压应力及喷丸后残余奥氏体的减少与齿轮表面应变对残余应力的影响,Inoue 等基于有限元法计算了渗碳直齿轮喷丸后的残余应力值。Astaraee 等在考虑齿轮复杂几何特征和梯度材料性能的影响,并忽略喷丸冲击热效应的前提下,建立了单丸粒喷丸模型,如图 4a 所示,采用改变喷丸角度的方法(喷射角变化范围为 0°~35°),对渗碳直齿轮齿面喷丸后残余压应力与粗糙度进行了有限元仿真,得到了 200%覆盖率下齿面米塞斯应力云图,如图 4b 所示。
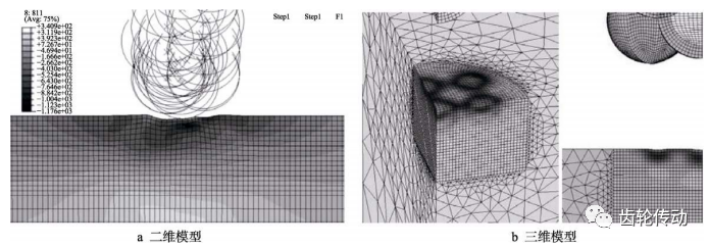
图3 齿根喷丸仿真
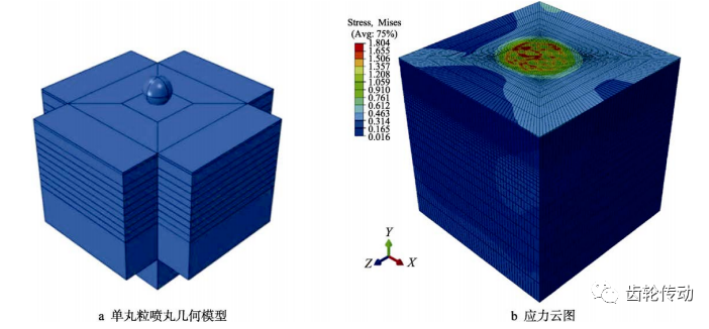
图 4 齿面喷丸仿真
通过对喷丸强化进行有限元数值模拟,建立喷丸工艺参数与喷丸强化质量表征指标的量化关系,从而实现喷丸强化工艺的优化设计,有助于改善喷丸效果。
但目前喷丸数值计算过程中存在一些不足之处:1)模型过于简化。齿轮齿根被简化为平面,而齿根的关键区域在齿根圆角处,并非齿底;仿真初始条件忽略渗碳诱导的初始应力场;仿真条件无法包含实际的喷丸工艺参数(喷枪个数、工作台转速、喷枪移动速度、弹丸形状等);喷丸工艺模拟属于热力耦合问题,仿真中忽略了热交换对仿真结果的影响。2)喷丸工艺参数(例如弹丸速度)有时是预设的,因而对喷丸效果只能进行定性分析。3)仿真内容单一。目前研究主要集中于应力场,其他物理场(例如组织场)的仿真研究鲜见报道。4)材料本构模型的精确创建及弹丸速度的确定难度较大。
目前喷丸仿真中比较常用的本构模型包括Chaboche 模型(各向同性,随动硬化)、Cowper-Symonds 模型(各向同性硬化,考虑应变率效应)、Johnson-Cook 模型(各向同性,考虑应变率效应、加工硬化效应、温度软化效应)等。其中,Johnson-Cook 模型形式简单且参数较少,在齿轮(或齿轮钢)喷丸工艺仿真中应用最为广泛。渗碳齿轮钢本构模型的选择,不仅要考虑弹丸冲击过程中材料受到的应变和应变率硬化影响、温度软化效应以及材料的循环特性等,还应考虑应变诱导马氏体相变的影响,因此受喷齿轮材料本构模型有待改进。同时,上述材料本构模型均属于大应变范围下的本构模型,对受喷齿轮高周疲劳问题相关研究(例如疲劳寿命估计)并不适用。
目前,弹丸速度确定的方法包括试验测试法(例如高速相机拍照测量、传感器测量、光学在线监测系统等)与经验公式法(例如利用 KIemenz 经验公式,通过阿尔门强度进行速度建模,通过弹坑尺寸进行速度预测)。其中,经验公式目前不具备普适性,有些公式只适用于特定喷丸设备、弹丸、阿尔门试片类型等。试验测量得到的弹丸速度可靠性更高,但无疑会增加测试成本。另外,齿轮具有复杂空间曲面结构,尤其是螺旋锥齿轮齿面法矢、曲率处处变化。喷丸工艺参数相同时,齿轮表面动态冲击力矢及升热效应不同,仿真过程中如果要进行简化处理,势必会导致误差的增加。因此,需借助其他软件(DEFORM、EDEM、YADE、ANSYS 等)进行动力学联合仿真,完善齿轮喷丸强化工艺数值模拟。
敬请关注下期内容:渗碳齿轮齿根喷丸强化研究现状与展望(二)