与普通齿形相比,双圆弧齿廓增加了齿轮的啮合对数,减少了普通齿轮啮合时尖点和干涉情况的发生,显著提高了齿轮的啮合效率。同时,其承载能力高,使用寿命长,可以在高速度、高负荷环境下工作。双圆弧齿轮是抽油机减速器的重要部件,使用一段时间后会不可避免地产生破损,直接报废更换新齿轮需要花费较高的费用。齿轮的破损形式主要有断齿、齿面剥落等。针对这些问题,目前的修复方案是对损伤程度较小、有修复价值的双圆弧齿轮进行激光熔覆或者对齿轮进行堆焊,由于修复后的齿轮齿廓不标准,必须对它进行切削加工,使再制造双圆弧齿轮恢复原有的使用性能及精度。
目前,许多学者对双圆弧齿轮不同的加工方法进行了研究,张晨玺验证了双圆弧齿轮数控加工的可行性,探索了圆弧齿轮数控加工工艺;郑江等人通过切齿实验在滚齿机上加工双圆弧齿轮,获得了新的双圆弧齿轮加工的有效方法;卢贤缵建立了双圆弧滚刀-齿轮空间啮合线方程,阐述了圆弧齿轮滚切瞬时成形的实质,并解决了滚刀设计中的各种理论问题。
以上研究可以实现再制造双圆弧齿轮加工目的,但加工效率过低,因此,本文作者设计一种能够对单齿或间隔破损的多个齿进行切削加工的机床。
一、单齿展成加工理论
双圆弧齿轮具有不可逆螺旋表面,因此只能采用分度切削。采用分度展成法对再制造双圆弧齿轮进行单齿加工,由于在加工过程中只需对单齿或间隔分布的几个齿进行切削,进给顺序规定为首先沿齿向进给然后沿齿形进给。
由运动学法原理可知,两齿面共轭的充要条件是接触点存在公切面,从物理概念上理解,若接触点处无公法线,且两啮合齿轮齿面处不存在接触点的相对移动速度矢量,那么两齿面会相互陷入或脱开,以致发生干涉现象并且降低齿轮传动的连续性。
运动学法原理的数学表达形式为

规定静止坐标系为 K 如图 1 所示,坐标系 Kd与齿条刀具固定,坐标系K1与被加工双圆弧齿轮固定。
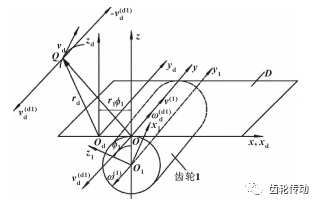
图 1 单齿分度展成瞬时回转法
双圆弧齿条方程如式 (2) 所示

由上述方程求得再制造双圆弧齿面接触点的法线矢量 n 为

由于进给顺序的特殊性,单齿分度展成加工需要考虑沿齿向进给速度。利用瞬时回转法求解瞬时接触点处相对速度,vd1d不在瞬时接触点 Q 处的位置,不能直接进行矢量的相加,需要将其移动到点 Q 处,为了保证原有的作用效果,在点 Q 处添加方向相反的速度矢量-vd1d ,- vd1d与点 O 处的 vvd1d构成速度偶 M d1d如式 (4) 所示:
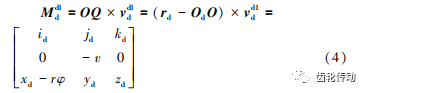
由此求得再制造双圆弧齿面接触点的速度矢量 v(d1)d 为

展开得

将式(3)和式(6)代入式(1)得到:

由此可知,单齿展成加工双圆弧齿轮满足共轭接触条件,单齿分度展成加工方法可行。
二、双圆弧齿轮及刀具参数
双圆弧齿轮参数
由于再制造后的齿轮齿廓不标准,对其切削加工后才能使用。该专用机床用于切削图 2 所示再制造双圆弧齿轮破损的单个齿或间隔破损的几个齿。双圆弧齿轮基本参数如表 1 所示。
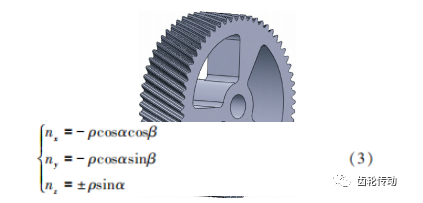
图 2 再制造双圆弧齿轮
表 1 双圆弧齿轮基本参数
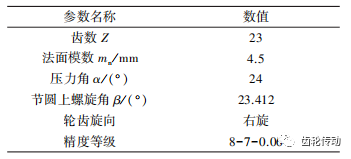
双圆弧盘形滚刀参数设计及模拟
双圆弧齿轮的齿廓较为复杂,是由数段圆弧通过一定的数学关系相接而成的完整的齿廓形状。
文中要加工的双圆弧齿轮法向模数为 4.5mm,根据国标 GB/ T 14348—2007 计算并设计的双圆弧盘形滚刀廓形如图 3 所示。
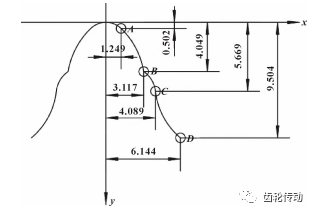
图 3 双圆弧盘形滚刀刀形
通过 MATLAB 软件编程,利用设计好的双圆弧盘形滚刀刀形模拟切削再制造双圆弧齿轮。将刀形先沿着螺旋线方向平移,再进行展成,得到了再制造双圆弧齿轮单个轮齿如图 4 所示,验证了该滚刀刀形切削再制造双圆弧齿轮的可行性。
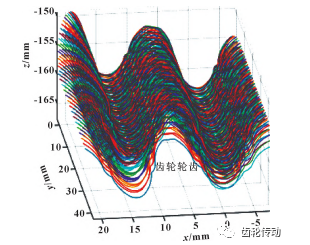
图 4 双圆弧盘形滚刀模拟切削单个轮齿
根据国标 GB/T14348—2007 可知:模数为 4. 5 mm 的双圆弧滚刀其外径为 112 mm,由此双圆弧盘形滚刀模型如图 5 所示。
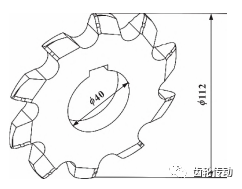
图 5 双圆弧盘形滚刀
三、再制造双圆弧齿轮单齿切削机床设计
机床传动原理分析
再制造双圆弧齿轮加工方法具有 4 个切削运动:双圆弧盘形滚刀的旋转运动、轴向螺旋进给运动、齿形方向展成进给运动和再制造双圆弧齿轮的旋转运动。因此切削机床传动原理主要由 4 条传动链构成,如图 6 所示。
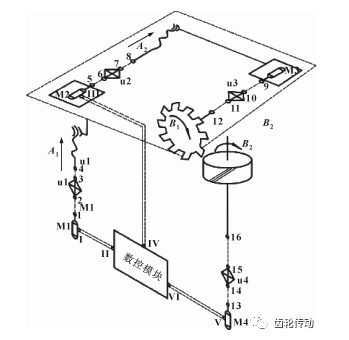
图 6 再制造双圆弧齿轮加工传动原理
(1)双圆弧盘形滚刀旋转传动链:电动机 M3-9-10-u3-11-12-双圆弧盘形滚刀。通过电机 M3 驱动,由换置装置 u3 带动双圆弧盘形滚刀旋转。改变换置装置 u3 的传动比可实现刀具转速的变速。
(2)轴向螺旋进给传动链:伺服电机 M1-1-2- u1-3-4-丝杠。通过步进电机驱动,由换置装置带动 丝杠与双圆弧盘形滚刀旋转传动链配合完成轴向螺旋进给运动。该传动链的进给速度参考加工再制造双圆弧齿轮的刀具切向切削速度。改变换置装置 u1 的传动比可实现螺旋进给的变速。
(3)齿形方向展成进给传动链:伺服电机 M2-5-6-u2-7-8-丝杠。通过步进电机 M2 驱动,由换置装置u2带动丝杠旋转,再带着刀具旋转传动链进行直线运动。齿形方向展成运动规律与齿轮齿条传动相似,因此该传动链的进给速度由工件转速决定。改变换置装置 u2 的传动比可实现展成进给的变速。
(4)再制造双圆弧齿轮的旋转传动链:伺服电机 M4-13-14-u4-15-16-工件。通过步进电机 M4 驱动,由换置装置 u4 带动齿轮旋转。螺旋角的形成使该传动链中工件旋转速度的确定依赖于齿向螺旋进给传动链的进给速度。改变传动链的换置装置 u4 的传动比可实现工件转速的变速。
再制造双圆弧齿轮单齿切削机床还设计了 3 条数控传动链。用于实现步进电机之间的数控联系,不仅确保滚刀沿螺旋线进给以及螺旋角符合设计要求,还保证了刀具与齿轮形成展成运动关系。
机床结构设计
再制造双圆弧齿轮单齿切削机床如图 7 所示,整个机床由刀具运动部件、齿向螺旋进给部件、齿形展成进给部件、工件运动部件、对刀部件以及机架构成。
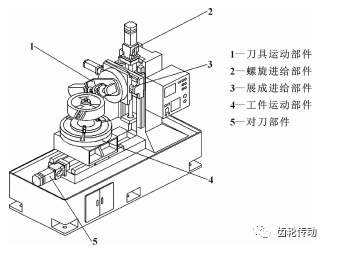
图 7 再制造双圆弧齿轮单齿切削机床
工件运动部件如图 8 所示,该部件可实现伺服电机驱动工件旋转。工件装卡底座由工件移动伺服电机驱动,可实现对不同尺寸齿轮的加工,以及精确控制盘形滚刀与齿轮的距离。齿轮回转由工件回转伺服电机驱动,通过蜗轮和蜗杆传递动力到齿轮夹具,保证了齿轮回转精度模芯的加工。考虑轴向齿距偏差的影响,在驱动工件旋转的伺服电机处设置减速器来减小轴向齿距偏差。
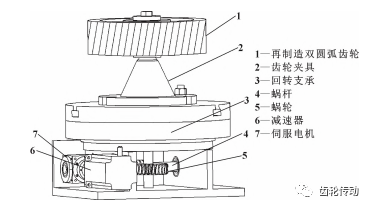
图 8 工件运动部件
四、机床加工误差分析
再制造双圆弧齿轮的加工误差是指通过单齿切削机床加工后,齿轮外形与理论设计的双圆弧齿轮外形之间的尺寸偏差,其大小直接影响再制造双圆弧齿轮的加工质量。下面主要讨论齿轮加工过程中沿螺旋线方向进给所产生的误差。
查找国家标准 GB/T15753—1995《圆弧圆柱齿轮精度》可得,对于加工过程中沿螺旋线方向产生的加工误差,圆弧齿轮轴向齿距偏差影响最大如图 9 所示。
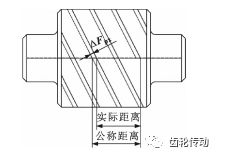
图 9 圆弧齿轮轴向齿距偏差
综合考虑驱动蜗杆所需提供的总转矩、安全系数及电机自身转子转矩后选择电机如表 2 所示。
表 2 电机基本参数
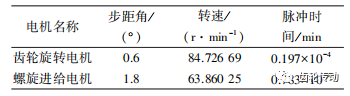
此时齿轮旋转的角度 θ1 为 0. 020 69°,滚刀螺旋进给速度为 2. 554 41 m/ min。每旋转一个步距角,滚刀沿轴向的位移 s2 为0. 199 9×10-3m,由螺旋角定义得

式中:θ1 为工件旋转角度,(°);R 为工件半径,m;a 为步距角个数;s2 为刀具位移,m;β1 为理论螺旋角,(°)。
将参数代入得a= 14. 396 7,取a2 = 14,代入式(8)得实际螺旋角 β2 = 24. 001 1°,产生了再制造双圆弧齿轮轴向齿距偏差。
再制造双圆弧齿轮轴向齿距偏差如图 10 所示,虚线和实线分别为理论和实际螺旋线。齿宽范围内,齿轮的轴向齿距偏差并不相同,所以计算齿轮的轴向齿距极限偏差 F′px很有必要,计算公式如式 (9):

式中:β1 为理论螺旋角,(°);β2 为实际螺旋角,(°);b 为齿宽,mm。
代入参数得 F′px = 40. 85 μm。
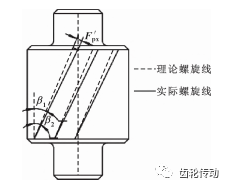
图 10 再制造双圆弧齿轮轴向齿距偏差
待加工再制造双圆弧齿轮齿宽 b 为 80 mm,根据抽油机减速器上使用的双圆弧齿轮精度要求,将再制造双圆弧齿轮加工机床精度等级设为 8 级,查找国家标准 GB/T15753—1995《圆弧圆柱齿轮精度》 可得,圆弧齿轮轴向齿距极限偏差 Fpx为 25 μm,不满足加工精度要求,因此在驱动工件旋转的电机处设置减速 比 ij 为 7.2 的减速器来实现减小轴向齿距偏差。
此时驱动工件旋转的电机旋转一个步距角,工件旋转的角度 θ′1为 0. 002 87°,代 入 式(8)得 a2=1. 999 5,取 a′2=2 代入式(8)得实际螺旋角 β′2=23. 388 1°,理论螺旋角 β1= 23. 411 7°,螺旋角误差进一步减小,代入式(9)得到 F′px=15. 51 μm<fpx=25 满足精度要求。
五、结论
根据一种先齿向再齿形的新的进给顺序,设计了再制造双圆弧齿轮单齿切削机床的整体方案。得到以下结论:
(1)根据运动学法原理和瞬时回转法验证了再制造双圆弧齿轮单齿加工的可行性,为后续机床设计提供理论基础。
(2)根据双圆弧滚刀的现有结构,设计出一种针对再制造双圆弧齿轮单齿加工的专用刀具。根据传动原理对刀具运动部件、齿向螺旋进给部件、齿形展成进给部件以及工件运动部件 4 个重要部件进行了设计,最终得到满足加工要求的再制造双圆弧齿轮单齿切削机床。
(3)对再制造双圆弧齿轮单齿加工误差进行分析,研究了减小再制造双圆弧齿轮轴向齿距误差的方法。
参考文献略.