RV 减速器具有精度高、回差小、刚性好、传动比范围广等优点,是机器人关节减速器的理想选择。摆线轮作为 RV 减速器中的核心部件,其加工质量及精度高低直接决定着 RV 减速器整机的传动精度。国内外学者针对 RV 减速器摆线轮的齿廓研究取得了一些研究成果。柯庆勋等对摆线齿轮在成形磨削过程中温度场的分布进行了仿真及试验研究; 王嘉宁等研究了摆线轮基本齿形参数与 RV 减速器啮合刚度的关系; 王文涛和徐宏海研究了摆线轮齿廓各参数对其传动性能的影响; 张跃明等对 RV 减速器中摆线轮齿形优化修形与参数化设计进行了研究,并进行了 RV 减速器摆线轮磨削工艺研究。对于齿轮的磨削,明兴祖等研究了面齿轮磨削加工工艺参数的优化; 郭辉等人阐述了采用六轴数控蜗杆砂轮磨齿机来磨削面齿轮的方法。上述涉及摆线齿轮加工的研究还不多。因摆线轮的齿廓形成复杂,在磨削加工中影响因素众多,且加工精度不易保证,而近年来随着我国机器人装备的快速应用发展,装备的高精运动要求又对摆线轮的加工精度提出了更高的要求,因此本文作者研究摆线轮齿廓精密加工后的表面质量特别是表面粗糙度的影响因素。
目前,摆线轮齿廓的磨削方法一般有成型法和展成法两种。成形法磨齿是将砂轮轴截面廓形修整为与摆线轮单齿齿槽具有相同廓形之后对轮齿齿面进行磨削加工的一种方法,由于其加工精度可达 4 级以上而被广泛用于齿轮齿面精加工。本文作者采用成形法对摆线轮齿廓进行磨削,并研究磨削参数对 20CrMnTi 摆线轮齿成型磨削加工后表面完整性的影响。
一、试验设计
试验采用的摆线轮材料为 20CrMnTi,其化学成分如表 1 所示,相应的机械性能如表 2 所示,摆线轮的几何参数及结构图分别如表 3、图 1 所示。试验机床为万能外圆磨床 M1432B-1000,磨削试验现场如图 2 所示,磨削方式为逆磨,采用水基乳化液冷却,砂轮采用单晶刚玉砂轮,粒度号分别为 60、100、150、220,中软级,陶瓷结合剂,单晶刚玉因抗破碎性较强、韧性大等优点,广泛用于韧性大、硬度高的材料表面加工中。


作者采用正交试验法,选正交表 L16 45 ,研究砂轮线速度、磨削深度、摆线轮的轴向进给速度及砂轮的粒度等 4 个因素对表面完整性的影响,选取磨削正交试验因素和水平如表 4 所示,砂轮转速 n 范围为 2 000~ 3 200 r/min,磨削深度 ap 范围为 0. 02 ~ 0. 12 mm,摆线轮进给速度 vf 范围为 1. 2 ~ 2. 8 m/min。正交试验结果如表 5 所示。试验中采用 Roughscan 高精度表面结构测量仪对摆线轮加工后的表面粗糙度进行测量,沿轴向进给方向等距选取 5 个部位测量,取样长度为 1. 0 mm,评定长度为 5. 0 mm,测量结果记入表 5 中。
二、试验结果分析
由表 5 可知,试验获得了表面粗糙度从 0. 23 ~ 0. 55 μm 的一系列摆线轮加工表面。从极差结果可知:对粗糙度影响最大的是砂轮粒度,其次是砂轮转速和磨削深度。影响最小的是摆线轮进给速度。进一步分析正交试验结果,得到 20CrMnTi 钢摆线轮外齿廓磨削加工后其表面粗糙度与砂轮线速度、摆线轮进给速度、磨削深度以及砂轮粒度的关系。
砂轮转速对摆线轮齿廓粗糙度的影响
将正交试验中砂轮转速对粗糙度的影响结果绘成图 3,从正交表和图 3 可以看出: 整体而言随着砂轮转速 n 的增大,磨削表面粗糙度 Ra 值会变小。其主要原因是随着砂轮对摆线轮齿面轮廓磨削能力的提高,砂轮与齿面接触迹线之间的摩擦力减小,相邻接触迹线间的轨迹距离变小,导致迹线的密度增大,因而摆线轮齿面粗糙度降低。且砂轮粒度为 60 目时获得的粗糙度普遍比粒度为 220 目的更大,因为粒度号越大,表明砂轮每单位长度上通过筛网孔眼的磨粒越多,磨粒尺寸就越小,对表面粗糙度越有利。
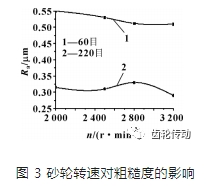
图 3 中,砂轮粒度为 60 目时,随着转速增加表面粗糙度缓慢变小,当粒度为 220 目时,表面粗糙度 Ra 值随转速增加呈波动性变小,即在 2 800 r/min 时稍有增加然后再变小,在 3 200 r/min 获得较小的表面粗糙度 0. 23 μm。这是由于砂轮线速度的提高会增加单位时间内磨粒切刃的切削次数,即减少磨粒切刃的单次切削时间,从而减小了相邻两磨削切刃切除材料后在加工表面留下的残留凸起高度,这样也有助于磨削热量的扩散,所以会导致表面粗糙度数值降低。
摆线轮进给速度对摆线齿廓粗糙度的影响
将正交试验中摆线轮进给速度对粗糙度的影响结果绘成图 4,可以看出: 无论粒度为 100 目还是 150 目,随着摆线轮轴向进给速度的增大,其表面粗糙度 Ra 的数值都会增加。其原因是随着摆线 轮进给速度的增加。在单位时间内磨削齿面的磨粒切刃数减少,使得单位面积齿面上形成的磨削残留高度增大; 此外,随着轴向进给速度的增加,磨床的颤振也有所增加,因而也会对摆线轮粗糙度产生一定的影响,使粗糙度数值有增大的趋势。

增大摆线轮进给速度与提高砂轮线速度的作用相反,它将使两相邻磨粒切刃之间切除的材料增多,且在加工表面上留下的残留凸起高度增大,从而导致表面粗糙度数值增大。
磨削深度对摆线齿廓粗糙度的影响
将正交试验中摆线轮进给速度对粗糙度的影响结果绘成图 5,可以看出: 随着磨削深度的增大,摆线齿面变得更加粗糙。这是由于磨削深度增加将使单颗磨粒的最大切削厚度增大,从而增大摆线齿面的塑性变形,使磨粒切削刃通过磨削工作区时在齿轮表面留下的切痕深度也增加,因此齿面粗糙度数值也会增加。

同时从磨削原理上分析,磨削深度的增加将使同时参与磨削的磨粒切刃数增加,导致磨削力增大,磨削温度升高很快,从而会降低磨削表面质量。但从上面试验结果来看,虽然整体上表面粗糙度数值会随磨削深度的增大而增大,但磨削深度的改变对表面粗糙度的影响并不是很明显。这是因为在实际磨削过程中,磨削用量是缓慢分次进给到最终磨削深度的,而并非是直接一次以磨削深度进行磨削。
砂轮粒度对摆线齿廓粗糙度的影响
由表 5 可知,砂轮粒度对表面粗糙度的影响最大,图 6 为根据试验结果绘制的砂轮粒度对表面粗糙度的影响关系。

从实验结果可知,摆线轮的齿面粗糙度随砂轮粒度号的增大而呈减小趋势。这是因为由于砂轮粒度越大,磨粒的直径尺寸越小,在砂轮表面单位面积上的磨粒个数越多,实际参加磨削的磨粒数增多,磨粒的出刃高度降低,从而使表面粗糙度数值降低; 同时,砂轮粒度越大,加工表面切痕的间距越小,划痕就越浅,从而也降低了表面粗糙度; 此外,由于同时参与磨削的磨粒个数越多,单个磨粒承受的磨削力就会越小,使表面粗糙度数值下降,也有助于提高加工表面质量。
三、磨削表面粗糙度的预测模型与试验验证
由上面分析可知,当砂轮粒度越大精加工效果越好,选取粒度为 150 目的砂轮采用不同的磨削参数进行试验,获得摆线齿轮磨削表面粗糙度数据,并对试验结果进行回归分析,采用幂函数形式进行粗糙度模型建模,可设

式中: K、α、β、γ 均为待定常数。
通过多元线性方程回归求解,可得式 (1) 中的 4 个待定常数,从而可得当砂轮粒度为 150 目时摆线轮齿面磨削表面粗糙度预测模型,如式 (2) 所示:

该预测模型范围为正交试验中的 3 个实验因素的范围。
为了进一步验证表面粗糙度预测模型的预测效果,将试验测量值与预测值进行比较,结果见表 6。

由表 6 可知,摆线轮齿面表面粗糙度预测值和实测值之间的相对误差在 1. 95% ~ 5. 1%之间,最大相对误差为 5. 1%,说明文中的摆线轮齿面磨削表面粗糙度的预测模型具有良好的预测效果。因此本文作者建立的表面粗糙度预测模型可为分析摆线轮齿面精密加工表面质量提供一定的理论参考。
四、结论
通过 20CrMnTi 钢摆线轮齿面磨削正交试验,分析了砂轮线速度、摆线轮进给速度、磨削深度以及砂轮粒度对摆线轮齿面表面粗糙度的影响规律,并在试验基础上建立了摆线轮齿面粗糙度的预测模型。结论如下:
(1) 砂轮粒度是影响摆线轮齿面磨削表面粗糙度最大的因素,砂轮旋转速度的影响作用次之,磨削深度的影响效果较小,摆线轮轴向进给速度的影响作用最小。
(2) 选用粒度较大的砂轮、提高砂轮旋转速度与减小磨削深度都能够降低表面粗糙度,摆线轮进给速度的增加整体上使表面粗糙度呈变大趋势,但变大效果不明显。
(3) 当使用 150 目粒度砂轮磨削时,在砂轮转速 n = 3 200 r/min、摆线轮进给速度 vf = 1. 2 m/min、 磨削深度 ap = 0. 12 mm 情况下,可使摆线齿面有更低的表面粗糙度、更好的表面质量。
(4) 预测模型具有较高的预测效果,表面粗糙度影响的预测模型和实测值的最大相对误差为 5. 1%,为实际加工合理选择磨削参数提供了试验依据和参考。
参考文献略.