行星滚柱丝杠副滚柱端齿轮为带有螺纹槽的渐开线直齿轮,与螺母固联的内齿轮相啮合。受螺纹槽的影响,齿面啮合接触应力与完整的直齿轮啮合接触应力不同。以行星滚柱端齿轮为研究对象,通过齿轮设计专业软件 KissSoft 和三维软件进行建模,利用有限元仿真软件分析带有螺纹槽的齿轮齿面接触应力分布和变化规律。研究表明,螺纹槽的存在增大了齿轮啮合的齿面接触应力,随着螺纹槽螺距的减小,齿面接触应力呈上升趋势,过大的螺距将减弱齿轮的抗弯强度。
行星滚柱丝杠副是一种将旋转运动转换为直线运动的机构,在螺母和丝杠之间的圆周上均匀分布有两端为直齿轮中间为螺纹的行星滚柱,两端直齿轮能够保障多个行星滚柱沿圆周方向均布和行星滚 柱轴线与丝杠轴线平行,确保行星滚柱丝杠能够可靠运行。与普通的滚珠丝杠相比,该丝杠副具备承载能力高、寿命长等优点,目前已被广泛应用于数控机床、工业机器人以及航空航天等领域。行星滚柱 中间段螺纹分别与丝杠和螺母螺纹啮合,两端直齿分别与固联于螺母两端的内齿圈啮合。在运动过程中,行星滚柱两端齿轮既需要与丝杠无干涉,同时也要与内齿圈啮合,因此行星滚柱两端齿轮需同时具备螺纹状结构和直齿轮形状结构。由于螺纹牙的存在,齿轮沿着齿宽方向不是连续的齿面,而是被分割成多个小齿牙,在单齿啮合区内,多个小齿牙同时参与内齿轮的啮合,如图 1 所示。为了分析这种不连续的齿面对齿面啮合接触应力的影响,本文基于 ANSYS 有限元分析对齿面啮合的接触应力进行仿真。

为提高端齿轮的承载能力,文献通过齿轮变位系数优化提升了螺纹滚柱齿轮的寿命和可靠性,并确定优化设计的目标函数,文献采用乘除法和模拟退火算法对行星滚柱丝杆副的齿轮部分结构参数进行了优化,上述文献从设计参数优化的角度提升了行星滚柱丝杠副齿轮内啮合的强度和寿命。文献基于 ANSYS Workbench 有限元软件对渐开线齿轮啮合进行了静力学有限元分析,得到齿轮等效接触应力云图和等效应变云图;文献基于 ANSYS 建立了滚柱齿内啮合的三维接触分析模型,得出小齿牙的存在会导致最大接触应力偏大的结论。以上学者的分析将对端齿轮齿面接触应力分析提供帮助。
一、直齿轮内啮合有限元分析
内啮合齿轮副参数
本文以瑞士 ROLLVIS SA 公司 RV 系列某型行星滚柱丝杠副参数为例,其内啮合齿轮副参数如表 1 所示。

本文通过 KissSoft 齿轮专业设计软件建立内啮合直齿轮的三维模型,并在 Inventor 三维软件中对内啮合直齿轮三维模型进行了结构设计。为降低有限元仿真计算量,此处截取了内啮合直齿轮一部分作为研究对象,具体结构如图 2 所示。通过调整外齿轮与内齿轮的相对角度,使两者的轮齿处于单齿啮合区域,便于分析在单齿啮合状态下齿面接触应力分布情况。

网格划分和边界条件设置
首先对齿轮材料进行属性定义。本文的齿轮材料均为不锈钢材料,密度 ρ 为 7 850 kg / mm3 ,弹性模量 E 为 200 GPa,泊松比 μ 为 0. 3,小齿轮为主动轮。
网格划分是有限元数值模拟分析的重要步骤, 影响数值计算结果的精确性,网格数量越多,计算精度也就越高,但计算量也会增大。为提高计算精度和减少计算量,本文截取了直齿轮啮合的部分模型, 并对齿轮单齿啮合区域进行了网格加密,确保了计算精度和计算量。齿轮在啮合过程中存在单齿啮合和多齿啮合交替变化的情况,此处对接触应力较大的单对齿内啮合进行有限元仿真分析。本文采用了适应性较强的四面体网格对齿轮进行网格划分,并对单对齿啮合区域进行了网格加密处理,网格大小为 0. 005 mm。网格划分情况如图 3 所示。

对外齿轮两端光轴设置 joint 连接,给外齿轮上的 joint 释放圆周方向的约束,并施加逆时针方向的扭矩,扭矩大小为 10 mN·m;内齿轮外圆设置 joint 连接,内齿轮的 joint 施加固定约束。
求解与后处理
运用 ANSYS Workbench 18. 0 软件对齿轮的接触应力进行分析,计算结果如图 4 所示。在齿轮的啮合位置处,齿面接触应力约为 55 MPa,且沿着齿宽方向应力分布较均匀。

二、不同螺距下螺纹槽端齿轮内啮合有限元分析
为研究不同螺距对行星滚珠丝杠的端齿轮内啮合接触应力的影响,本文对螺距分别为 2 mm,3 mm, 4 mm,5 mm 的带螺纹槽的滚柱端齿轮(以下分别简称 RV2、RV3、RV4、RV5)齿面接触应力进行有限元计算。根据几何关系,行星滚柱两端的端齿轮齿顶圆直径不得大于中间螺纹滚柱的顶径。因此,端齿轮的齿顶圆直径在不同螺距下是不同的。滚柱的顶径 dra 和底径 drf 计算如下:

式中:Hr 为滚柱牙高;ds 为丝杠轴的公称直径;Ps 为丝杠轴的导程;Pr 为滚柱的导程;dr 为滚柱的公称直径。
带螺纹槽端齿轮参数
本文通过以上公式计算了行星滚柱端齿轮的外形尺寸参数,不同螺距下的外形尺寸参数如表 2 所示。与端齿轮啮合的内齿轮参数不变,具体参数见表 1。
求解与分析
本文对不同螺距的端齿轮设置相同的边界条件,均与直齿轮内啮合设置的边界条件保持一致。经过有限元数值仿真计算,得到了不同螺距下的齿面接触应力云图,如图 5~图 8 所示。
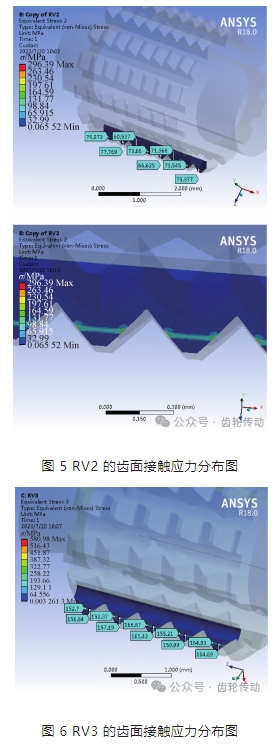

对比图 5 和图 4 应力云图,螺距为 2 mm 的齿轮齿面接触应力明显高于不带有小齿牙的直齿轮,并且每个小齿牙的齿面应力呈两边高中间低的趋势。螺纹牙的存在,使齿轮啮合时的接触线明显变短,导致接触应力增大;带有小齿牙的外齿轮与连续齿面的内齿轮在啮合的过程中,在小齿牙和螺纹槽过渡部分齿面应力发生突变,导致应力集中,使小齿牙齿面应力呈两边高中间低的分布趋势。
从图 5~图 8 可以看出,随着螺距的增大,齿宽方向上小齿牙数量随着螺距的增大而减少,同时在单齿啮合区域内,齿轮啮合的接触线也相应变短,导致外齿轮与内齿轮在啮合时齿面的平均接触应力呈上升趋势,承载能力下降。
将不同螺距下的齿根部分的应力分布处理成 3D 云图,得到如图 9~图 12 的结果。


从图 9 至图 12 中可以看出,相较于连续齿面的外齿轮齿根应力分布云图(见图 4) ,齿根部分 (齿高 1. 4 mm 至 1. 6 mm 之间) 应力分布呈波浪状,波峰数或波谷数与齿宽方向的小齿牙数相同, 且随着螺距的增加,外齿轮齿根部分波动幅度就越大。这是由于螺纹将齿轮分割成多个独立的小齿牙,齿轮在啮合过程中,有小齿牙的齿轮根部应力值较大,形成波峰;在螺纹槽对应的齿轮根部由于没有小齿牙参与啮合,齿根部分应力值较小,形成波谷。随着螺纹螺距的增加,螺纹的小径减小, 即螺纹底径更接近外齿轮的根部,齿轮在啮合过程中,有小齿牙的根部需要分担的抗弯拉力就增大,导致应力值增大,螺纹槽对应的齿根部分需要分担的抗弯拉力减小,应力值相应减小,最终导致齿根部分应力分布波动幅值增大。这种波动幅值增大现象将不利于齿轮的承载,在设计行星滚柱丝杠螺距时,在螺距较大的情况下需要校核齿根抗弯强度,防止小齿牙齿根断裂失效。
三、结 语
本文以行星滚柱丝杠滚柱端齿轮内啮合为研究对象,考虑到螺纹槽将齿根分割成多个小齿牙,齿面啮合应力分布发生变化,采用有限元仿真分析方法对齿轮静态内啮合进行了分析,该分析方法可为带有螺纹槽的齿轮参数设计和强度计算提供参考。仿真分析得到如下结论:
1)行星滚柱端齿轮的齿面接触应力要高于连续齿面齿轮的接触应力,且随着螺纹螺距的增大, 啮合线变短,齿面接触应力也相应增大。每个小齿牙的齿面接触应力分布呈两边高中间低的分布趋势。
2)行星滚柱端齿轮的齿根部分应力分布呈波浪状,且波峰数或者波谷数与齿宽方向的小齿牙数相同。随着螺纹螺距的增加,齿轮齿根部分的应力分布波动幅值就越大。
3)对螺距较大的行星滚柱,需要校核端齿轮的齿根抗弯强度,防止齿轮断裂导致行星滚柱丝杠失效。
参考文献略.