齿轮作为各类传动系统的核心关键零件,常工作在高速、重载、腐蚀性强的环境中,其表面质量对整个系统的使用性能有着至关重要的影响。齿轮钢材料常通过热处理等方式达到表面强化的目的,其淬硬表面可达HRC58~62,属于难加工材料,在普通磨削加工中存在着磨削力大、表面易烧伤、工具易磨损等问题。基于此,本文对齿轮钢材料淬硬表面的磨削性能进行研究,以期为制定磨削加工工艺提供技术支持。
超声振动辅助磨削技术是一种集普通磨削与超声加工于一体的高性能复合加工技术,近年来快速发展,在提升难加工材料加工效率、改善加工质量等方面显示出积极效果。Bhaduri 等对比了 SiC 砂轮和金刚石砂轮在超声振动条件下对钛铝金属间化合物的磨削加工效果,结果表明,超声振动可以降低 35% 的磨削力,工件表面粗糙度降低 10%。Nik 等采用数学建模、有限元分析和遗传算法相结合的方法,对超声装置进行了设计、优化和制造,并开展了超声振动辅助磨削 Ti–6Al–4V 试验,比较了常规磨削和超声磨削工艺的磨削力和表面粗糙度,结果表明,超声条件下 Ti–6Al–4V 的磨削力更小,表面质量更好。Wei 等通过建立微破碎产生区域比例计算模型和信息尺寸模型分析了旋转超声振动辅助磨削条件下工程陶瓷表面微破碎的轮廓大小,结果表明,超声振动的施加降低了表面破碎的尺寸,提高了表面质量。鉴于当前将超声辅助加工技术应用于磨削齿轮钢淬硬表面的研究较少,开展齿轮钢淬硬表面超声振动辅助磨削研究工作对提高齿轮表面质量有重要意义。
本文对比了淬硬齿轮钢 AISI 9310 和轴承钢 GCr15 的超声振动辅助磨削加工性。通过搭建齿轮钢淬硬表面超声振动辅助磨削试验平台,设计单因素试验研究磨削加工工艺参数对磨削力、表面粗糙度的影响规律及作用机制,并分析了磨削表面微观形貌及其影响因素,为制定超声振动辅助磨削加工策略奠定基础。
一、试验及方法
试验材料及装置
试验所用工件材料为渗碳淬火齿轮钢 AISI 9310 和淬火轴承钢 GCr15,其化学成分如表 1 所示。通过电火花线切割加工(WEDM)制备尺寸为 30 mm×10 mm×12 mm 的工件。其中,10 mm 为砂轮宽度方向,30 mm 为工件进给方向,12 mm 为磨削深度方向,30 mm×10 mm 即为平面磨削试验表面,且在试验前通过铣削将该表面粗糙度降低至 Ra0.8 μm,如图 1 所示。图 2 为试验前工件表层 / 亚表层的硬度分布,在距表层 500 μm 的深度内, 两种钢材料热处理后的硬度能够达到 HRC60~65。


试验装置如图 3 所示。磨削试验采用 BLOHM Profit MT–408 高速精密平面成形磨床,其最大输出功率为 45 kW,最大转速为 8000 r/min,并配有冷却系统。砂轮采用已广泛用于磨削淬火钢的白刚玉砂轮,牌号为 WA80F6V35M,其最大线速度为 35 m/s,磨粒粒度为 80#,外径为 400 mm,宽度为 20 mm。工件通过螺栓固定于自研的超声振动平台上,将该平台连接至超声电源并设置频率为平台的谐振频率 19.6 kHz,以产生平行于工作台进给方向的高频振动。此外,在调节超声电源功率的同时,利用单点激光测振仪 LV–S01 测量工件的振幅,如图 4 所示,两种材料的实际振幅与超声电源输出功率呈现良好的线性关系,在试验中通过控制超声电源功率使振幅为 6 μm。此外,磨削环境非常复杂,磨削过程中工件周围被冷却液覆盖,导致无法采集到磨削过程中的动态振幅信号,所以本研究中采用了无磨削热力负载条件下的振幅值。

试验条件及方案
为探究齿轮钢 AISI 9310 淬硬表面超声振动辅助磨削加工性,设计以磨削 3 要素为变量的单因素对比试验,即砂轮线速度 vs、进给速度 vw 和切深 ap。所有试验均采用顺磨的方式,在试验过程中,交替关闭和开启超声电源以实现普通磨削和切向超声磨削。每组试验前,使用相同的磨削参数对工件进行平整,并使用单点金刚石笔对白刚玉砂轮进行修整,以确保试验条件的一致性。具体的试验条件如表 2 所示。

试验中的磨削力经由 Kistler 9253B 型三向压电测力仪采集,后通过 Kistler 5080A 型电荷放大器放大电信号,最终在计算机软件上进行显示和处理。选取 3 次稳定磨削阶段力信号的平均值作为文中的磨削力值。对工件表面质量检测前使用无水乙醇对已加工表面进行清洗并干燥,加工后表面粗糙度 Ra 采用 MAHR M2 型手持式粗糙度仪进行测量,检测时,使金刚石触针处在垂直于被测表面的上方,并做垂直于磨削方向的运动。为使测量数据更加准确,在每个被测表面区域内各随机测量 3 次,取其平均值作为最终表面粗糙度的数据。表面微观形貌特征采用 Quanta 200 型扫描电子显微镜进行表征。
二、结果与讨论
磨削力及其经验公式的建立
磨削力常用于描述磨削过程和分析磨削机理,反映了加工期间砂轮与工件之间的相互作用,是评价材料磨削性能的一项重要指标,与材料本身力学性能、磨削工艺参数、加工装备等都有着密切的关系。本文采用平面磨削,轴向力可忽略不计,且磨削参数中的切深较小,测力仪力系与实际磨削力力系间无须转换,即由测力仪测得的 y、z 两个方向的力为切向磨削力 Ft 与法向磨削力 Fn。
淬硬钢平面磨削过程中,磨削参数对切向磨削力和法向磨削力的影响规律如图 5 所示。超声磨削降低磨削力效果显著(图 5(a)),随着砂轮线速度从 15 m/s 增大至 30 m/s,普通磨削和超声磨削的法向和切向磨削力均呈减小的趋势,与普通磨削相比,超声条件下,GCr15 与 AISI 9310 的切向磨削力最高降低 13.64% 与 15.04%,法向磨削力最高降低 14.08% 与 9.1%;如图 5(b)所示,随着进给速度从 4 m/min 增大至 10 m/min,普通磨削和超声磨削的法向和切向磨削力均呈增大的趋势,与普通磨削相比,超声条件下,GCr15 与 AISI 9310 切向磨削力最高降低 20.51% 与 13.17%,法向磨削力最高降低18.91% 与 10.87%;如图 5(c)所示,随着磨削深度从 10 μm 增大至 25 μm,普通磨削和超声磨削的法向和切向磨削力均呈增大的趋势,与普通磨削相比,超声条件下,GCr15 与 AISI 9310 切向磨削力最高降低 19.07% 与 17.36%,法向磨削力最高降低 14.08% 与 14.6%。张洪丽指出,切向超声振动对单颗磨粒切削深度的影响甚微,但切向超声振动的断续磨削特性能够提高砂轮磨粒的微破碎,使磨削过程中磨粒切削刃一直锋利,实现了磨削力的降低。此外,GCr15 作为高碳铬钢,有较多的网状和片状渗碳体组织,且 Cr 元素含量高导致磨削温度升高后伴有二次硬化的作用,因此其磨削力高于低碳钢 AISI 9310。

磨削力数学模型的建立能够预测在不同磨削条件下的加工性能,从而有利于找到最佳的磨削工艺参数。磨削力由法向和切向两部分组成,在本次试验中两者的变化趋势相同,并且本次试验测得的磨削力符合一般磨削的基本规律,测量数据可靠,本文以法向磨削力为目标,建立经验公式以指导加工参数的选择。根据经验公式的普适模型可表达为

通过对等号两边同时取对数得到多元线性回归方程,即
从本次 10 组试验所得的法向磨削力数据中,取出 9 组作为样本数据,经统计回归后得到两种淬硬钢表面法向磨削力经验式(3)~(6)。
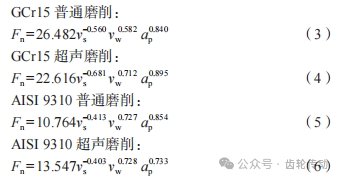
如表 3 所示,将最后一组试验参数代入经验公式,对比计算值与试验值,可见其误差均在 10% 以内,说明所建立的法向磨削力数学模型与试验数据拟合度较好。此外,普通磨削的误差小于超声磨削,这是由于超声条件下磨粒常因冲击产生随机破碎,仅考虑 3 个输入变量的经验公式不足以描述磨削力与磨削参数间的关系。若误差过大则可以考虑采用神经网络法,处理超声磨削中复杂的输入输出关系,以指导磨削加工用量的制定。
磨削力比与比磨削能
与磨削力相同,磨削力比也是评价磨削过程中材料磨削性能的重要指标。图 6 显示了材料去除率对磨削力比的影响。普通磨削中力比的变化范围较大,GCr15 和 AISI 9310 在普通磨削中力比的变化范围分别是 1.79~2.02 和 1.74~2.01,而在超声磨削中力比则较为稳定,变化范围分别是 1.82~1.89 和 1.82~1.87,显示出白刚玉砂轮在超声磨削淬硬齿轮钢时优良的磨削性能。当材料去除率为 1 mm3 /(mm·s)时,超声磨削中砂轮磨粒因受到冲击而破碎,其磨损程度大于普通磨削中砂轮的正常磨损,导致超声磨削力比大于普通磨削;当材料去除率为 2.5 mm3 /(mm·s)时,普通磨削中砂轮磨损加剧,GCr15 和 AISI 9310 表面的磨削力比分别增大 11.07% 和 15.71%,而超声磨削力比变化不大,且比普通磨削减少了 8.46% 和 7.04%。由此,证明了超声振动辅助磨削工艺有助于增大磨削加工参数,并将材料去除率提高了 2.5 倍,提高了加工效率。

比磨削能 es 作为磨削过程中最重要的物理量之一,由磨削力与加工工艺参数推导而来,反映了去除单位体积工件材料的过程中所消耗的能量。图 7 显示了材料去除率对比磨削能的影响,GCr15 与 AISI 9310 淬硬表面的比磨削能曲线由最小二乘法拟合得到,可表示为式(7)~(10)。

可以看出,AISI 9310 的比磨削能在多数条件下小于 GCr15,说明 AISI 9310 淬硬表面的磨削性能好于 GCr15 淬硬表面。两种材料在普通磨削与超声磨削条件下,随着材料去除率的增大,比磨削能均呈现降低的趋势。当材料去除率为 1 mm3 /(mm·s)时,GCr15 普通磨削与超声磨削的比磨削能分别为 124.08 J/mm3 和 100.14 J/mm3 ,AISI 9310 普通磨削与超声磨削的比磨削能分别为 106.47 J/mm3 和 103.77 J/mm3;当材料去除率增大至 2.5 mm3 /(mm·s)时,GCr15 普通磨削和超声磨削的比磨削能分别降低至 77.96 J/mm3 和76.47 J/mm3 ,AISI9310 普通磨削和超声磨削的比磨削能分别降低至 81.72 J/mm3 和75.63 J/mm3 ,这是由于尺寸效应造成的,是材料硬化和热软化效应综合作用的结果。材料去除率较小时,磨粒的钝圆半径与最大未变形切厚的比值较大,在成屑前磨粒反复挤压待加工表面,磨削区材料应变硬化起主要作用,比磨削能较大。此外,高频振动的引入实现了砂轮的微破碎,从而提高了砂轮的自锐性,使得超声磨削的比磨削能始终小于普通磨削,改善了材料的磨削性能。
表面粗糙度与表面微观形貌特征
工件表面粗糙度是衡量磨削加工表面完整性的一个重要指标。磨削参数对表面粗糙度的影响规律如图 8 所示。超声磨削能够降低表面粗糙度,如图 8(a)所示,随着砂轮线速度从 15 m/s 增大至 30 m/s,表面粗糙度呈减小的趋势,超声条件下,GCr15 与 AISI 9310 表面粗糙度最高降低 7.39% 与 9.47%;如图 8(b)所示,随着进给速度从 4 m/min 增大至 10 m/min,表面粗糙度呈增大的趋势,超声条件下,GCr15 与 AISI 9310 表面粗糙度最高降低 8.62% 与 6.41%;如图 8(c)所示,随着磨削深度从 10 μm 增大至 25 μm,表面粗糙度呈增大的趋势,超声条件下,GCr15与AISI 9310 表面粗糙度最高降低 7.79%与7.03%。表面粗糙度 Ra 与已加工表面的材料残留高度有关,切向超声振动辅助磨削中砂轮对工件反复熨烫,有助于降低表面粗糙度。

图 9 为加工后工件表面的微观形貌。在热、机械复合作用条件下,普通磨削中存在较大范围的材料断裂、破损、再沉积及涂覆等表面缺陷(图 9(a)和(c));与普通磨削相比,超声加工表面呈现出良好的表面纹理,无明显的表面损伤(图 9(b)和(d))。磨削表面形貌是由砂轮上的众多磨粒对工件表面进行摩擦、耕犁、切削等综合作用的结果。磨粒通常被认为具有负前角的 特性,磨屑从前刀面流出,图 10(a)显示了负前角切削时的金属流动。如图 10(b)所示,普通磨削中磨粒不断接触工件,导致冷却液无法进入前刀面,前刀面的热量增加,材料的塑性流动作用增强,磨屑容易黏附在砂轮表面,产生再沉积缺陷,未成屑材料黏附在加工表面上,产生涂覆缺陷。此外,由于砂轮的挤压,冷却液中混入的大尺寸磨屑及破碎磨粒相当于游离磨料,容易对已加工表面造成材料的断裂、破损等缺陷。超声磨削中磨屑及破碎磨粒的尺寸更小,并且通过磨粒和工件的周期性分离改变冷却液的流场,及时带走热量和磨削产物。因此,超声振动中断续磨削和往复熨烫的特性可以改善加工表面缺陷,有利于提高工件表面完整性。


三、结论
(1)超声振动辅助磨削因其断续磨削和往复熨烫的特性,能有效降低磨削力和比磨削能,且随着材料去除率的增大,超声磨削力比更加稳定,有助于提高材料的磨削加工性、增大磨削加工参数并提高加工效率。
(2)利用本次试验数据建立的经验公式可以预测白刚玉砂轮磨削 GCr15 与 AISI 9310 淬硬表面时的法向磨削力大小,误差在 10% 以内。
(3)当磨削速度、工件进给速度和磨削深度分别为15 m/s、8 m/min 和 15 μm 时,与普通磨削相比,GCr15 和 AISI9310 淬硬表面切向超声振动辅助磨削条件下表面粗糙度降低了 7.39% 和 9.47%,且加工表面无缺陷,提高了工件表面完整性。
参考文献略.