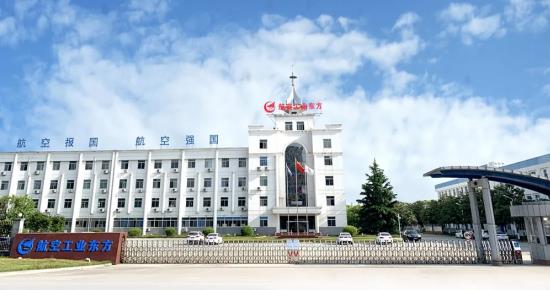
图1:航空工业东方是航空工业机载的下属企业。
长度33米,集成14台设备,全自动化排产与生产……一走进陕西东方航空仪表有限责任公司(以下简称航空工业东方)的厂区,映入眼帘的这条超大规模、高度智能化的柔性产线令人慨叹。作为航空工业航电系统下属企业,肩负着多项国家军事装备工程任务的重点机载设备生产商,航空工业东方一直在产品质量上有着显著优势,而其自筹资金大力投入智能制造更是为持续走在行业前列蓄足了动能——该条生产线凭借在设备、夹具上的大胆创新,柔性、智能、数字化的前瞻设计,被誉为我国航空工业智能化升级的典型代表之一。
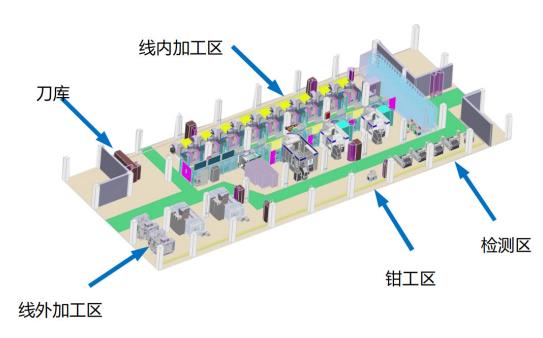
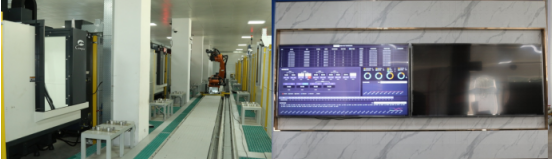
图2:航空工业东方的柔性生产线总长33米,集成了13台加工中心和1台清洗设备,可实现自动排产生产,目前已经能够同时生产6-8种不同类型零件,设备利用率提升了40%以上。
“从针对零件铣削加工的智能单元,到涵盖多个生产工序的智能产线,再到如今覆盖40余种不同零件、按工艺流程全要素以MES系统整合线内线外数十台套加工、检测设备的柔性生产网络,经历了多次方案迭代,我们的技术团队才最终完成了该条生产线的设计、调试与投入运行。”航空工业东方副总经理张海东介绍说道。
新需求与旧生产模式的矛盾
航空零件结构复杂、品种多、精度高、批量小,往往需要技术工人与自动化设备“打配合”,这样的生产方式对技术工人的操作水平要求高,人工成本大且加工效率低。在航空工业东方厂内,这种高需求与旧生产模式之间的冲突也曾每天上演:过渡依赖人工,加上频繁换刀、装夹找正、机器停机等造成的时间浪费,让厂里的设备利用率仅为30%左右,严重影响交付时效。由此,航空工业东方决定搭建一条柔性产线来提高生产率。
作为资源与产品在多品种、多平台、多设备间变化流转的关键接口,也是贯穿整个生产链的重要工序,装夹系统的改造优化是整个工程的重点。要知道在原有的生产模式中,零件的每次装夹固定都需要操作人员在机床内部人工找正,然后用压板压紧;产品换型时频繁地换装、找正、固定,不仅增加设备停机时间,还极易影响定位精度、降低产品品质的稳定性。
此条柔性线当前主要用于加工多品类液压壳体零件。同时,基于对产线使用机器人上下料、自动化排产的需求,航空工业东方的技术团队提出应用零点定位系统来重构工装的对接技术,在多方比较后,选择了与在航空制造领域有着丰富经验的德国雄克公司合作。
“在调研之前,我们就已经接触过零点定位系统,对其在效率、精度提升上的优势有一定了解。雄克公司是零点定位系统的行业领先者,其产品的高精度、高夹持力,都是我们所需要的。更重要的是,我们希望通过雄克技术团队丰富的行业经验与定制化服务,让产线可持续优化、让潜能发挥到最大。” 张海东说道。
智能装夹是自动化生产的必要基础
“雄克已帮助国内多个客户打造过多条柔性生产线,根据我们的经验,项目实施中,夹具的通用性、可扩展性、以及过程稳定性对产线的运行起着至关重要的作用。”雄克中国项目负责人,产品应用经理程训杰表示。航空工业东方的挑战更胜一筹,不仅要连接多个品牌的机床,并且对夹具的精度要求极高。对于雄克而言,需要提供容纳全局的整套解决方案,不仅仅是标准件。因此在项目初期,雄克技术人员做了大量基础性工作。锁定智能化生产与快速换型的目标,设计了针对性的夹持方案——零点快换系统+虎钳。
该产线中所集成的14台设备都配置了带有两个雄克VERO-S零点快换模块的基座,通过零点快换系统的快速定位、自锁夹紧等功能,能够在数秒内对工件托盘或机床中配有拉钉的工件进行夹持。模块自带的夹紧检测功能,以及小于0.005mm的重复定位精度,更为产品加工时的安全性、产品品质的稳定性提供了可靠保障。在实际加工中,装夹操作可以在机床外完成,无需停机的优势进一步提升了机床利用率、提高了加工品质。
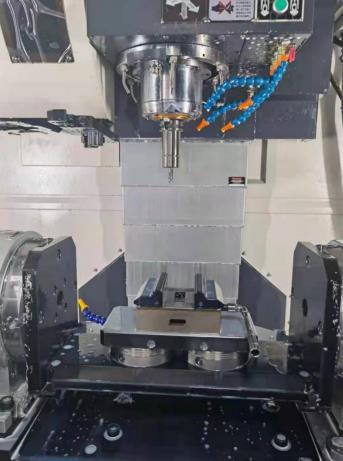
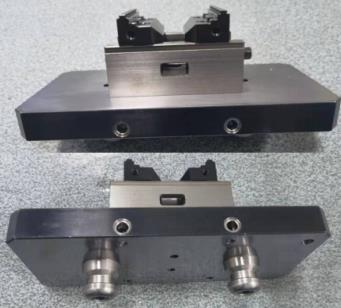
图3:航空工业东方柔性生产线中所集成的14台加工中心都配置了带有两个雄克VERO-S零点快换模块的基座,并针对具体零件在工件托盘上安装了虎钳工具,以实现工件的快速装夹、换装,从而确保了产线的顺畅运行,并提升了生产效率与产品品质的稳定性。
零点快换系统成功的关键在于标准化接口。在配合生产线运行时,它可作为机床和夹具之间的接口,即插即用,大大节省机床装夹时间;在配合机器人使用时,它又变成工件与机器人的接口,实现自动上下料需求;在产品换型时,接口仍然通用,对于机床而言,零点模块就是夹具的固定接口,产品的换型对零点以下部分没有任何影响。
柔性线能实现自动传输、高效运行,很大程度是因为其能将原本用于物料/工件流转的“非有效加工时间”转变成用于生产的“有效生产时间”。零点快换系统解决了流转中接口不一的问题,虎钳则用来解决更为细致的工件夹持问题。
“东方航空仪表生产线选择的是雄克的KSC高精度手动虎钳,夹持范围广,适合产品尺寸变化较大的夹持需要,并且KSC虎钳配套全密封主轴,适用于复杂环境的加工,比如粉尘、切削液、铝屑等环境,这些优势特别适合东方航空仪表的加工需求。”程训杰介绍说,“产品毛坯时在机外装夹到虎钳上,虎钳和产品组合后变成一个整体,经由上料工位、粗加工机床、半精加工机床、精加工机床、清洗机,可一直流转到工序结束,直至工件下线。机床端的零点配置是一样的,机器人的抓取端设计也是一样的,雄克零点快换的标准接口是构成这样一条柔性线的基础。大幅提升了效率,维护也很简单。”
张海东补充道:“灵活性、可流动性的工装方案,是柔性生产线高效率的基本条件,也是产线能够实现自动排产、生产的关键。”在航空工业东方对产线的精准定位、高效管理,以及在包括雄克智能装夹产品在内的众多高精度、高可靠度设备协同运作的保障下,目前该条柔性线已经能够同时加工6-8种不同类型零件,机床利用率相比之前提升了40%以上,效率几近翻倍。
“零点定位系统实现了工艺基准与测量基准的统一,从而为柔性生产线的精度控制提供了基准统一的解决手段。零点定位和高精度虎钳的组合在小批量多品种零件加工中,实现了工装的柔性和复用,这是符合前沿发展趋势的、极具实用性的解决方案了。”来自南京航空航天大学的李亮教授对航空工业东方的这一智能装夹手段给予了充分的肯定。
数字化智能制造的精密布局
除了生产操作本身的自动化,该条柔性线的高度智能还体现在诸多方面。基于零件工艺的自动排产:不同于传统加工工序的排产方式,航空工业东方技术团队基于自身对零件工艺的深度把控,将排产的重点落实在零件各个特征,这一决策在提升加工效率的同时也确保了加工品质;全数字化网络:不仅是线内的设备,航空工业东方利用MES系统等将线外的多台设备与线内贯通连接,形成了一个规模庞大的数字化网络,实现了生产管理层面的智能化;线边库:柔性线内创新集成了一个用于存放未完成零件或已加工完成零件的线边库,以应对急单、插单情况,也提升了生产线的灵活度、敏捷性……
据介绍,柔性线还在不断的升级完善中,在该条线上加工近40种零件外,还计划将质量控制系统等集成在内,这一过程也离不开工装产品的支撑。“我们的工装方案也在随着柔性线的发展不断完善,例如针对航空产品质量高需要随时检测的需求,我们会将工装方案拓展至检测环节,用零点定位系统高精度的定位功能,将生产与检测工序间原本繁琐的换装、找正时间进一步压缩。”程训杰补充介绍道。
“高柔性的智能化生产线在零件精度高、结构复杂且批量小的航空制造领域并不多见,当航空工业东方技术团队找到雄克寻求装夹解决方案并介绍产线时,我们也被航空工业东方这种敢于创新的精神所鼓舞。”程训杰感叹道,“无论是细节处的专注、对每一个定制化装夹方案的优化验证,还是大方向上的远见,对于‘数字化智能制造’的精密布局,我们都为能与如此优秀的团队合作,能参与这样一条具有跨越性意义的航空制造项目而倍感荣幸。”