近年来,随着国防军工、航空航天、生物工程和医疗器械等高端技术领域需求的快速增长,机械制造业正朝着精密化、微细化、柔性化以及智能化方向发展,这对加工制造的水平提出了更高要求。集机、光、电、控制等多学科融合的超精密微细加工技术代表了加工制造的最高水准,其不仅与国防工业和高新技术的发展密切相关,还决定了国家在激烈国际竞争中的话语权,因此,世界各国对此都十分重视。
超精密微细加工技术的进步很大程度上依赖机床行业的发展,经过三十多年,我国机床行业已具备相当规模,但国内机床产业大而不强,机床产品主要集中在低、中端领域,高档数控机床产品仍主要依赖进口,竞争力相对较低,尤其是作为国家战略制造装备的超精密加工机床的技术水平十分薄弱。《中国制造2025》将高档数控机床提升到需要大力发展的战略高度。
机床被誉为“工业母机”,是整个装备制造业生产的核心基础。超精密加工机床科技含量和精密程度高,在精密微小复杂自由曲面加工方面具有显著优势。虽然国内很多机床企业也能生产五轴联动机床,但核心部件仍需外购,在众多核心技术领域仍是空白。
制约我国机床水平提高的因素有很多,一是基础科学方面,材料性能不达标,生产工艺不完善,结构设计不合理,使得零部件性能达不到要求,可靠性差;二是控制、测量技术方面,国内现有的机床运动模型与机床系统的兼容性、通用性差,传感器灵敏度低,测量装置精度低,限制了机床自身的精度。攻克高端数控机床的“卡脖子”技术、彻底解决核心技术的“阿喀琉斯之踵”是我国机床行业乃至整个制造业由大变强的必经之路。
2 超精密加工机床
目前将加工精度0.1~0.01μm、加工表面粗糙度0.04~0.005μm的加工称为超精密加工。超精密加工机床是实现超精密加工的首要基础条件,而超精密机床的精度指标尚无统一标准,工业界达成的共识是参照20世纪90年代由美国Union Carbide公司、Moore公司和美国空军兵器研究所等制定的“POMA”计划,将进给分辨率达到0.005μm、主轴回转精度达到0.02μm、定位精度达到0.05μm、直线度精度达到0.02μm、综合精度达到0.1μm的机床称为超精密加工机床。
从国家战略的角度来看,掌握超精密加工核心技术能引领高端加工制造业的发展,并在激烈的国际竞争中取得先机。因此世界各国从上世纪开始纷纷布局,制定战略来重点发展超精密加工技术,如上世纪50年代开始,美国出于在航天、国防等领域发展需求,率先开始超精密加工技术的研究,20世纪80年代,美国军方制定了“先进制造技术开发计划”,英国先后制定了“NION国家纳米技术计划”、“LINK纳米计划”,日本制订了“ERATO先进技术探索研究计划”等。美、英、日、德、瑞士等国家对超精密加工技术研发的持续投入也加速了其在民用领域的产业化进程,上世纪80年代开始,美国的摩尔(Moore)、普瑞斯泰克(Precitech),日本的芝浦(Shibaura)、发那科(Fanuc),德国吉德曼(Gildemeister)等企业陆续推出了超精密加工机床,并开始投入民用产品制造,逐步实现了超精密加工机床的商品化,但在这一时期大部分超精密加工机床为专用机床。从90年代开始,超精密加工机床的核心技术(例如检测系统、控制系统、驱动系统、精密导轨与轴承等)已逐渐发展成熟,并且汽车、相机、光学仪器等商品的普及极大提高了人们对超精密加工技术的需求,从而促使超精密加工机床成为民品领域较为常见的加工设备。
1980年,美国摩尔(Moore)公司开发的M-18AG型超精密非球面加工车床引领超精密加工技术进入亚微米级,该机床采用气浮导轨、空气静压轴承、空气隔振弹性支承以及优质铸铁床身,并配备双频双坐标激光测量系统及恒温系统,使得加工精度可达0.3μm,加工直线度可达0.5nm/mm,加工表面粗糙度低至7.5nm。随后该公司先后推出了以Nanotech 250UPL、350UPL、500FG为代表的超精密加工设备,其中,三轴超精密加工机床Nanotech 250UPL(见图1a)采用模块化设计,可以将B旋转轴和Y直线轴进行拆卸更换,其X,Z直线轴行程为200mm,回转半径最大可达125mm,通过配备超精密伺服车削系统,使得最小分辨率达到0.01nm,加工表面粗糙度小于2nm,面形精度小于0.1μm;五轴数控机床Nanotech 350FG可以进行超精密磨削和单点金刚石车削,其直线轴采用液体静压导轨,稳定性高,使得直线轴最小分辨率达到0.034nm,重复定位精度300nm,主轴径向和轴向跳动量小于13nm,重复定位精度±1arc/s,如图1所示。
为满足国防需求,从20世纪60年代起,美国开始了超精密加工机床的研究历程,美国劳伦兹实验室(LLNL)先后开发了DTM-1、DTM-2超精密加工机床,并于1983年成功研制出DTM-3卧式大型超精密光学加工车床,其刀架采用摩擦驱动,配备液体静压导轨和轴承,并搭载激光干涉仪,使得加工精度可达13nm,加工表面粗糙度达到7.6nm。

图1 Nanotech 系列超精密加工机床
20世纪80年代,美国率先开始进行激光核聚变研究,为制造超大型激光器(NIF)所需的大口径光学元件,美国国防部投资1300万美元成功研制出大型光学元件超精密金刚石切削车床LODTM,其加工直径可达Φ1.625m,如图2所示,该机床具备快速电致伸缩微进给装置(FTS)、激光在线测量系统、空气隔振系统和超高精度温度控制系统,在1.6m的加工范围内径向加工误差28nm,直线度误差小于0.025μm,加工表面圆度和平面度小于12.5nm,加工表面粗糙度小于4.2nm,代表了超精密加工的最高水平。

图2 LODTM立式大型光学金刚石车床
英国Cranfield精密工程研究所(CUPE)是欧洲超精密加工高水平的代表,也是世界精密工程研究中心之一,其在1991年为加工X射线太空望远镜镜筒而研制的OAGM2500大型六轴数控超精密磨床(见图3)配备了精密数控驱动系统和双频激光测量系统,该系统X,Y轴最大行程为2500mm,Z轴最大行程为610mm,X,Y轴配备液体静压轴承,Z轴和专用探测头采用空气轴承,平面加工精度可达1μm,加工表面粗糙度可达2nm。为了满足车削和研磨的使用要求,CUPE于1991年又成功研制出Nanocentre250、Nanocentre600等多款非球面零件超精密加工机床,该系列机床通过配备高刚度的液体静压轴承和伺服驱动系统,最小分辨率可达1.25nm,加工表面粗糙度小于10nm,面形精度小于0.1μm。

图3 OAGM2500大型超精密磨床
美、英研制的DTM-3、LODTM和OAGM2500三台机床代表了超精密加工的世界最高水平。相较于美、英等国,日本的超精密加工技术起步较晚,但发展迅猛,其发展路径与美、英相比明显不同,日本超精密加工的研究主要针对民用产品,如精密测量仪器、医疗器械、微电子以及光学元件等,这种研究方向也决定了日本的超精密加工机床具有小而精的特点。20世纪90年代,日本东芝机械成功研制的ULG-100A(H)超精密非球面复合加工机床,通过同时控制两个旋转轴(刀具轴和工件轴)可以实现非球面光学透镜模具的切削和磨削加工,其X轴(刀具轴)最大行程150mm,Z轴(工件轴)最大行程100mm,由于配备了空气静压轴承和高精度位置反馈光栅,使得旋转轴分辨率可达10nm。丰田工机研制的具有车、磨复合加工功能的AHN05、AHN10、AHN60-3D等超精密加工机床可以实现3D自由曲面的超精密切削、磨削加工,通过配备无铁心直线电机、频闪仪、亚微米精度光栅等,使得加工表面粗糙度可达16nm,表面精度可达0.35μm。
除美、英、日外,德国、瑞士等国家在超精密加工领域也在不断加大投入,均进入了世界第一梯队。
3 超精密加工机床典型结构
超精密加工机床的类别与普通机床相似,可以从不同角度进行划分:按照通用程度可划分为通用型和专用型,如普通超精密加工车床、磁盘超精密加工车床等;按照加工工艺方法可分为超精密加工车床、超精密加工铣床、超精密加工磨床、超精密抛光机床以及超精密复合加工中心等;按照设备的复杂程度,超精密加工机床可以从两轴扩展到五轴。
3.1 两轴联动超精密加工机床
两轴联动超精密加工机床是结构最简单的超精密加工机床,如卧式超精密车床、超精密飞切机床等。图4为Precitech公司研制的Nanoform L1000两轴联动超精密车床。

图4 Nanoform L1000两轴联动超精密车床
其X,Z直线轴呈T形安置在机床底座上,主轴布置在X轴导轨上,刀具则布置在Z轴导轨上,在X,Z直线轴的相互配合下,同时在主轴的旋转带动下,利用高精度圆弧刃金刚石刀具可实现非球面曲面等回转类零件的超精密加工,该机床直线轴采用静压油轴承导轨,配合对称的直线电机布置,可实现0.01nm的编程分辨率,其加工表面粗糙度<1.25nm,形状精度<0.125μm。
用于大口径KDP晶体抛光的超精密单点金刚石飞切机床是一种可实现纳米级超精密切削加工的两轴联动超精密加工机床。哈尔滨工业大学研制的超精密单点金刚石飞切机床的结构如图5所示,在进行飞切加工时,工件固定在工作台上,通过调节Y轴预先设定好切削深度,Z轴以低速缓慢进给的方式移动,主轴驱动飞切盘从而带动刀具对工件进行切削加工。所有运动轴均采用空气静压轴承支撑,直线轴采用直线电机,旋转主轴采用力矩电机直接驱动,运动精度极高,机床床身配备空气弹簧,可以对环境振动等干扰进行有效控制。该机床可以直接将光学晶体、有色金属等材料加工到镜面水平,适用于光学零件的大批量生产。
3.2 三轴联动超精密加工机床
三轴联动超精密加工机床最基本的特征是有且只有三个运动轴可以实现联动控制。三个联动轴可能是X,Y,Z三个直线轴的组合,也可能是旋转轴和直线轴的组合。如美国Moore公司研制的Nanotech 350UPM高效超精密微磨削/微铣削机床(见图6),X,Y,Z三个直线轴均采用全约束箱式油静压轴承滑轨,Y轴(垂直轴)采用双线性电机驱动并配备空气轴承自适应平衡器用于优化伺服性能,所配置的空气轴承磨削主轴转速可达60000r/min(配有液体致冷),编程分辨率可达0.01nm,该机床适用于对非球面曲面和微沟槽等结构进行微细铣削加工,可以得到传统机床无法达到的光学表面精度和粗糙度。

图5 超精密单点金刚石飞切机床
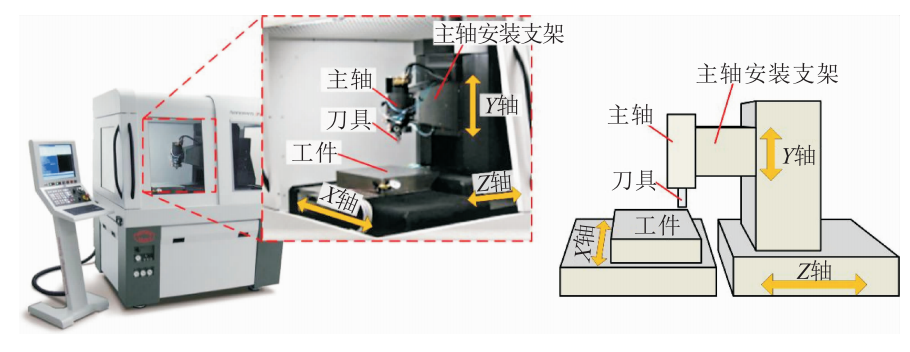
图6 Nanotech 350UPM三轴联动超精密机床
图7为一种包括2个直线轴和1个旋转轴的三轴联动超精密车床,该机床的旋转轴采用双驱模式,既可作为普通旋转主轴进行速度闭环控制,又可作为角度伺服轴进行角度位置闭环控制。
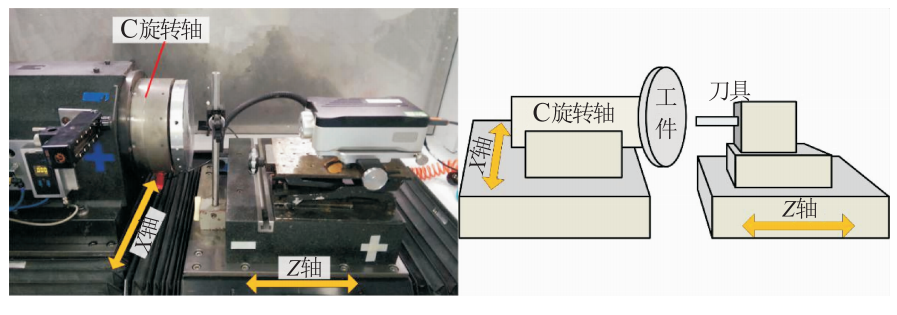
图7 X,Z,C三轴联动超精密车床
3.3 四轴联动超精密加工机床
四轴联动超精密加工机床通常是在三轴联动超精密加工机床的基础上增加一个联动轴扩展的超精密加工设备。为满足不同产品的加工技术要求,生产厂商通过产品的模块化结构设计,发展同系列和跨系列变形品种,从而衍生出不同结构的多轴超精密加工机床。如Moore公司研制的Nanotech 450UPL系列超精密加工机床,通过改变模块化结构,可以适应各种球面和非球面部件的加工,通过增添可拆卸Y轴模块形成了X,Y,Z,C结构的四轴联动超精密加工机床(见图8b);通过增添B旋转轴模块、主轴单元等,形成了X,Z,B,C结构四轴联动超精密加工机床(见图8c)。
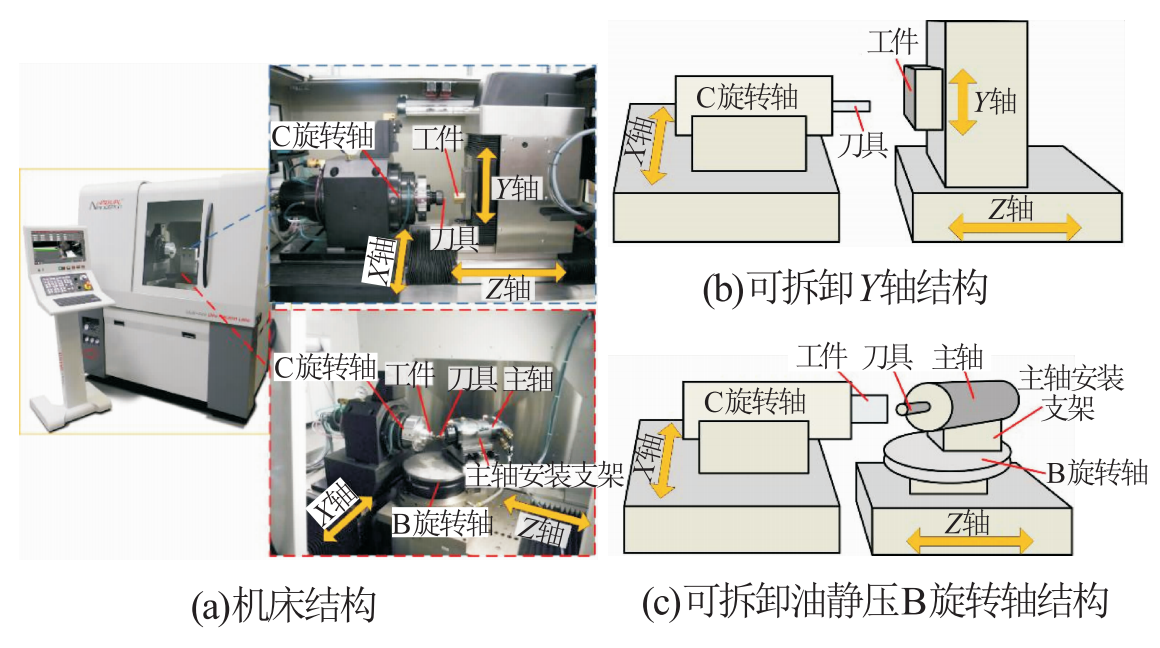
图8 Moore Nanotech 450UPL超精密加工机床
机床所有运动轴均采用全约束油静压闭式导轨,主轴采用多孔石墨空气静压轴承,由无刷直流电机驱动,最大转速为10000r/min,轴向/径向运动精度可达12.5nm。机床线性分辨率可达0.01nm,角度分辨率可达(0.1×10-7)°,其加工表面粗糙度可达纳米级,轮廓精度达到亚微米级。
3.4 五轴联动超精密加工机床
五轴联动超精密加工机床是在三轴联动超精密加工机床的基础上,通过增加两个联动轴来实现自由曲面高精加工。2001年,瑞士米克朗公司推出的HSM400U高速五轴联动加工中心(见图9)在汉诺威EMO机床展上正式亮相,成为世界上第一台真正的五轴联动超精密加工机床。此后的二十年间,为适应不同的市场需求,各种五轴联动超精密加工机床被相继开发。
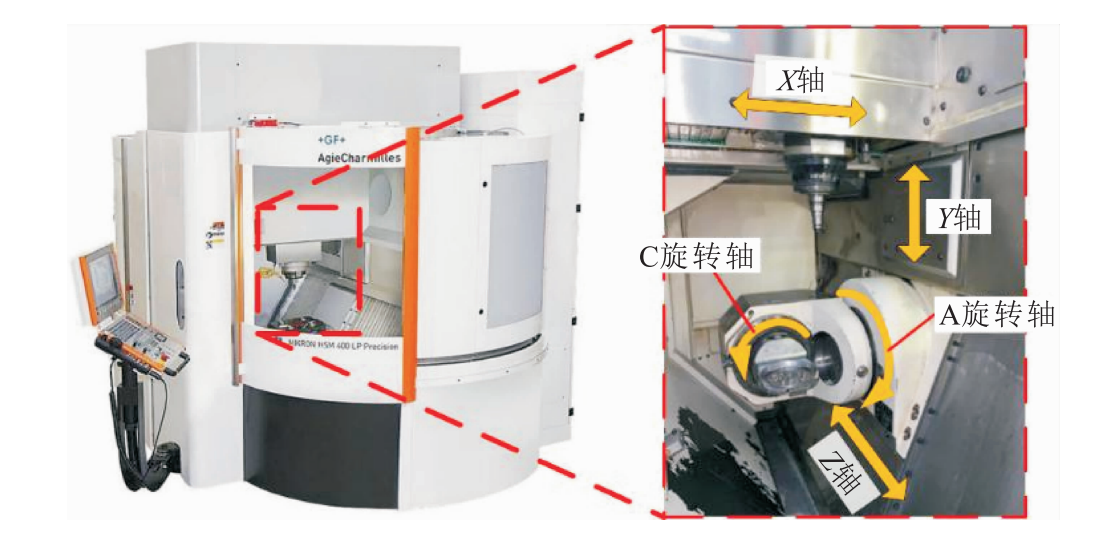
图9 HSM400U五轴联动超精密加工机床
目前,市场上主流的五轴联动超精密加工机床包括3个平动轴(T)与2个旋转轴(R)的组合,根据旋转轴在机床中的布局,五轴超精密加工机床可分为三个基本类型(见图10)。其中,单摆头—单转台结构(RTTTR)中,一个旋转轴(摆动轴)在主轴端,一个旋转轴(回转轴)在工作台端,由于两个旋转轴分别在机床的两条运动链上,因此工作台刚度较好,尺寸无限制,适用于加工小型零件,多应用于中、小型五轴超精密加工机床上。
图10a为FANUC Robonano α-0iB RTTTR型五轴超精密加工机床,其所有的运动轴均采用空气静压轴承,直线轴采用直线电机驱动,旋转轴采用内装伺服电机驱动,能够实现1nm的步进分辨率。双转台结构(RRTTT)机床的两个旋转轴均在工作台一端,也称为“摇篮式”结构,如图10b所示,该结构机床主轴刚性较好,加工效率高,与单摆头—单转台结构相比,在相同的行程内加工范围更大,但由于需要实现工作台摆动,所以其负重往往有严格的限制,多用于加工中、小型零件,如中小型叶片、涡轮等。双摆头结构(TTTRR)的五轴超精密加工机床如图10c所示,两个旋转轴均位于主轴端,由于双摆头自身尺寸较大,考虑加工范围的需要,一般会做成龙门式,因此该结构更适合加工大型零部件,如机身、机翼等。

图10 五轴联动超精密加工机床典型结构
3.5 超精密加工机床关键零部件
不同种类的超精密加工机床虽然结构有所差异,但功能部件基本相同,包括旋转轴、平动轴、主轴单元、切削刀具、工作台及机床床身等,其中,旋转轴、主轴单元和切削刀具是对超精密微细自由曲面加工影响最大的关键零部件。
旋转轴是多轴超精密加工机床的重要组成部分,其运动精度对非自由曲面的加工精度影响较大。增加旋转轴使得机床在灵活性和高效性方面具有明显优势,但引入旋转轴使机床的机械结构更为复杂。目前,超精密加工机床旋转轴系统常采用液体或气体等流体介质悬浮轴承,减振性好且磨损小,但刚度较差,运动精度更易受到GEs、FIEs、热诱导误差、加工颤振等因素的影响。
主轴单元是超精密加工机床的关键部件之一,按照动力来源主要分为以下两种:
一种是电主轴,受散热条件、稳定性等多种因素的限制,目前商业化的电主轴转速大部分在50000~150000r/min,个别达到300000r/min。如Moore公司推出的Nanotech系列超精密加工机床,以无刷直流电机驱动,采用多孔质材料节流气体静压轴承,最高转速可达60000r/min,回转精度小于12.5nm。广州昊志机电股份有限公司的DQF-400气体静压电主轴,最高转速可达400000r/min,回转精度小于2μm,主要用于PCB转孔加工。
另一种是气动涡轮主轴。如FANUC公司推出的Robonano系列五轴联动超精密加工机床,采用空气静压轴承气动涡轮主轴,其最高转速可达60000r/min,回转精度约为0.05μm。Precitech公司的Nanoform系列超精密加工机床采用气动涡轮主轴,其最高转速可达80000r/min,回转精度小于0.03μm。采用气流驱动与空气轴承支承的涡轮式主轴受益于气体低温升、低摩擦系数和高流速,主轴转子可达到极高的回转速度,但随着转速升高,跳动误差也会不断增大。此外,静压承载力、转子质量、流体均匀性等对气浮涡轮主轴的承载性能和回转精度都会产生影响。
微细刀具是超精密微细加工中刚性最薄弱的环节,其尺寸大小、几何结构、材料性能等对加工尺寸、切削质量和加工精度都有很大影响。微细刀具尺寸决定了加工零件尺度,通常微细刀具的直径小于1mm,如果微细刀具的直径能进一步减小,则微型零件尺寸也必将减小,甚至能逼近蚀刻技术所能加工的尺度。目前,通过聚焦离子束加工技术,可以加工出直径小于50μm的微型立铣刀。然而,在微细加工中,所设定的每齿进给量可能小于刀具刃口半径以及刀具—刀架—主轴系统的跳动量,受尺寸效应、未变形切削厚度、微尺度材料性能等因素影响,微细加工机理与传统加工之间存在较大差异。在超精密微细加工过程中,微细刀具与加工工件直接接触,微细刀具的这些特性会导致加工过程的稳定性较差,从而出现较大的加工误差。
为满足柔性化的加工需求,许多超精密加工机床都进行了模块化设计,为便于机床在不同模块之间相互切换,设计出许多专用连接装置,例如图6、图8c、图10a所示的主轴安装支架,极大提高了主轴拆卸、更换的便利性。该类连接装置提高机床整体灵活性的同时,也会改变机床结构的刚度,引入装配误差,从而影响机床的加工性能。
总体来说,超精密加工机床的零部件制造精度、装配工艺水平等已经达到了目前技术的最高水平,从理论上讲,若能准确、有效地控制这些机床关键零部件所产生的误差,将进一步提升超精密加工机床的加工精度。
我国从上世纪50年代就开始了针对超精密加工技术的研究,但在70年代后才重视其发展。1958年,上海机床厂自主研制出我国第一台高精度磨床,一举打破国际垄断;1987年,北京机床研究所成功研制出能够进行球面加工的空气轴承主轴超精密加工车床,然后又成功研制出超精密加工铣床和超精密数控车床,提升了我国超精密加工的水平。但这一时期,我国仍没有开发出能够进行非球面加工的超精密加工机床,与国外相比还存在较大的差距。“九五”期间,北京机床研究所研制的NAM-800纳米级超精密数控车床的反馈系统分辨率达到2.5nm,机械进给系统可实现5nm的微进给,使得直线轴直线度达到0.15μm/200mm,主轴回转精度达到30nm,加工表面粗糙度达到8nm。同时,哈尔滨工业大学、国防科技大学、北京航空精密机械研究所等高校、科研机构在超精密加工技术领域也在不断取得进步。
4 超精密加工机床发展趋势
超精密加工机床作为国家重要的战略物资,已经成为体现一个国家制造业最高水准的代表之一,发展趋势如下:
(1)高效、精密
高精度与高效率是机械加工所追求的两大目标。当前,超精密复合加工技术,如化学机械抛光、磁流变抛光等,虽能加工出具有极高表面完整性和表面质量的工件,但耗时长、加工效率低。而高速车削、铣削加工技术虽然加工效率高,但无法获得上述复合加工工艺所能达到的加工精度。探索高效加工基础上的误差补偿与控制技术以及高精加工基础上的高效加工技术,进而开发出全新的超精密加工设备成为超精密加工领域的研究目标。
(2)智能化、无人化
智能制造是制造业未来发展的主流方向,通过提高加工设备的智能化水平可以降低对人工经验的依赖,甚至完全代替人工,这也是制造业不断追求的目标。智能制造依赖于人工智能、类脑技术等新兴技术领域的发展,智能网络技术、实时在线监测诊断技术等是未来智能化加工机床必须具备的核心技术,也是提高产品质量和生产效率的重要保障。
(3)复合式、通用化
在激烈的市场竞争中,高效生产已经成为企业的生命线。在此背景下,诸如“以铣代磨”、“以磨代研”以及“以磨代抛”等跨等级加工工艺的需求不断提高,此外,能够同时具备车、铣、刨、磨等功能的通用复合式机床成为市场研发的重要方向。
(4)极大化、极小化
为满足航空航天、武器装备等领域所需大型光学器件等的加工要求,需要研发大型超精密加工设备。同时,为满足微型电子机械、光电信息等领域所需微型器件(如微型传感器、微型驱动元件)的加工需求,需要研发微型超精密加工设备(并非加工微小型工件一定需要微小型加工设备)。因此,超精密加工设备需要向大型化、微型化两极发展。
(5)绿色节能
“碳中和”、“碳达峰”是提高我国经济全球竞争力的重要战略,也是我国对世界的承诺。加快降低碳排放步伐,探索高效节能的新型加工方式、降低切削液的使用、提高材料利用率、引导绿色技术创新是制造业的发展趋势。
5 结语
超精密加工技术已经渗入人们生活各方面,鉴于军事、信息等产业对高精度零部件件的巨大需求,我国超精密加工机床虽已取得长足的进步,但与生产实际要求相比,与国外还有一定差距,这一局面在短期内仍无法改变,因此我国应加大对超精密加工机床研究的持续投入,不断进行知识技术储备,力争打破高端超精密加工设备被国外垄断的局面。