1、自动变速器的总体分类
自动变速器可以按照多个标准进行分类,比如按速比变化是否连续或换挡时动力传递是否中断等。然而传动装置是自动变速器的核心,按所采用传动装置的不同对自动变速器进行分类是进行自动变速器技术分析的基础。
自动变速器的分类方式和类型
分类方式
|
类型
|
按速比变化方式
|
有级式、无级式
|
按换挡时动力是否中断
|
动力换挡式(换挡动力不中断)、非动力换挡式(换挡动力中断)
|
按采用的传动装置
|
液力变矩器与齿轮组合式、带-轮摩擦式、离合器与定轴齿轮组合式
|
照传动装置的不同,汽车自动变速器在进化过程中逐步出现了液力变矩器与齿轮传动组合式、带-轮摩擦式、主离合器与定轴齿轮传动组合式等三种主要形式。三种形式的自动变速器具有各自不同的结构和工作原理,因而在成本、性能等方面各具特点。
各种传动形式自动变速器的的传动装置、换挡方式和特点
形式
|
代表类型及名称
|
传动装置
|
换挡方式
|
特点
|
|
液力变矩器与齿轮传动组合式
|
液力式机械变速器AT(AutomaticTransmission)
![]() |
液力变矩器+行星齿轮组
|
摩擦原件(离合器或制动器)搭接控制
|
+换挡品质好;结构复杂;控制难度大;传动效率低
|
|
带-轮摩擦式
|
无级式变速器CVT(Continuously Variable Transmission)
![]() |
液力变矩器+行星齿轮+钢带-锥形轮
|
改变锥形轮半径
|
一定范围内速比连续变化,无顿挫感;传动效率低;转矩容量有限
|
|
主离合器与定轴齿轮组合式
|
机械式自动变速器AMT(Automated Manual Transmission)
![]() |
离合器+ 定轴齿轮组
|
主离合器控制+同步器开关控制
|
结构简单、传动效率高、换挡动力中断,平顺性差、
|
|
主离合器与定轴齿轮组合式
|
双离合器变速器DCT( Dual ClutchTransmission)
|
湿式DCT(Wet DCT-WDCT)
![]() 干式DCT(Dry DCT-DDCT)
![]() |
双离合器+定轴齿轮组
|
同步器预先结合,双离合器搭接控制
|
传动效率高、换挡品质好、控制难度大、结构较复杂
|
2、变速器的发展情况
液力变矩器与齿轮传动组合式以液力式机械自动变速器(Automatic Transmission, 简称AT)为主要代表。
AT 通常由液力变矩器、行星齿轮系、多个摩擦结合原件(离合器、制动器)和相应的电控系统所组成,依靠摩擦结合原件间的搭接控制实现动力换挡。AT 自20 世纪30 年代推出以来不断更新换代,20 世纪末6 挡AT 诞生,德国采埃孚(ZF)公司于2009 年推出了8 挡AT 并装备于多款高级轿车上,目前9 挡AT 也已接近量产。AT 具有技术成熟,工作可靠,换挡品质较好的优点,目前仍占有世界上大部分自动变速器的市场份额,其缺点是传动效率较低、控制难度大、结构复杂、对相关产业链要求较高。
带-轮摩擦式变速器是汽车用无级式自动变速器(Continuously Variable Transmission,简称CVT)的主要代表,目前CVT 主要是指带-轮摩擦式CVT。
CVT 依靠传动带与带轮的摩擦传递动力,通过连续改变带轮的工作半径使传动比在一定范围内连续变化。1958 年荷兰DAF 公司开发出橡胶带CVT,20 世纪70 年代中后期,荷兰VDT 公司又推出了金属带CVT,其后金属带的结构得到不断改进,CVT 的可靠性和耐久性也在不断改善,20 世纪末CVT 逐渐市场化。CVT 变速平顺、操纵方便,但由于依靠摩擦传动,受限于所能传递的转矩,目前只能应用于中小型乘用车,在大型乘用车和商用车上无法得到应用,且CVT 仍需要液力变矩器和齿轮传动机构,结构和制造较为复杂。
主离合器与定轴齿轮传动组合式以机械式自动变速器(Automated ManualTransmission,简称AMT)和双离合器式变速器(Dual Clutch Transmission,简称DCT)为主要代表。
AMT 保持了MT 的机械传动结构基本不变,由控制机构自动完成换挡过程中对于离合器和选换挡装置的操纵,继承了MT 结构紧凑、传动效率高、工作可靠的优点,对各种车辆具有广泛的适用性。
全自动AMT 在20 世纪80 年代已开发成功,但由于存在换挡动力中断,换挡品质的提高受到限制,因而目前主要应用在燃油经济性要求较高的小型乘用车和商用车上,在乘坐舒适性要求较高的中高级乘用车上的应用较少,但近年来由于其高效节能的优势,AMT 又逐渐引起了人们的兴趣。DCT 可以看作是AMT 的一种变形,其采用了类似于两套AMT 系统交替工作的模式,两套AMT 系统分别负责奇数挡位和偶数挡位的传动。DCT 在2003 年左右正式推向市场,目前正在快速发展,可靠性、耐久性不断提高,适用范围不断扩大。通过双离合器的搭接控制,DCT 实现了动力在奇数挡和偶数挡之间的无动力中断切换,克服了AMT 换挡动力中断缺点的同时,也产生了控制难度大、工作可靠性降低、生产成本高等问题。
自动变速器的发展历程
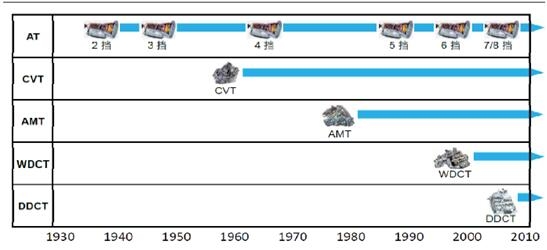
现在自动变速器已经形成了AT、CVT、AMT、DCT 等多条技术路线协同发展的格局,随着电子控制技术的进步和材料性能的提升,4 种类型自动变速器仍在持续的改进和优化,未来或许还将有其它类型的自动变速器出现。
自动变速器的生产制造技术掌握在通用、福特、克莱斯勒、大众、本田、丰田、PSA 等世界主要汽车公司及其控制的非独立供货商和德国采埃孚(ZF)、德国格特拉克(Getrag)、美国伊顿(Eaton)、日本加特可(Jatco)等少数独立供货商手中。
3、变速器的性能分析
自动变速器的各项性能是由所采用的传动装置和换挡方式决定的。由于传动装置和换挡方式不同,各种自动变速器的性能也有很大的差别。
自动变速器中应用的传动装置主要有液力变矩器、金属带-锥形轮、行星齿轮系和定轴齿轮系这4 种类型。
液力变矩器以液压油为工作介质,是一种非刚性转矩变换器。液力变矩器的输入轴与输出轴间靠液体联系,工作构件间没有刚性联接,因而能消除冲击和振动,具有较好的过载保护性能和起动性能,但传动效率较低、质量大、成本高。
液力变矩器原理图
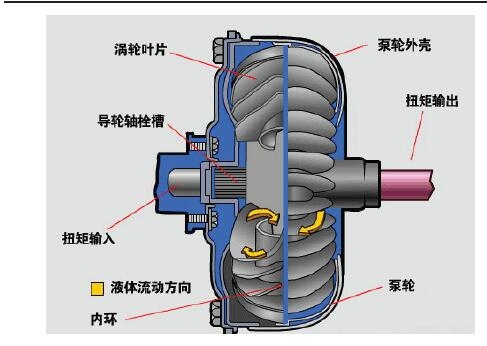
带-轮变速传动原理图
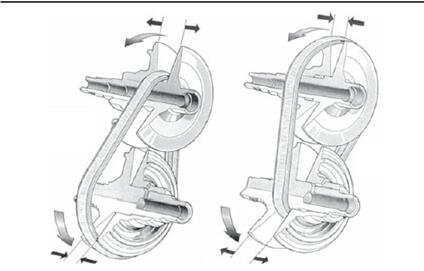
CVT锥形轮工作半径的改变
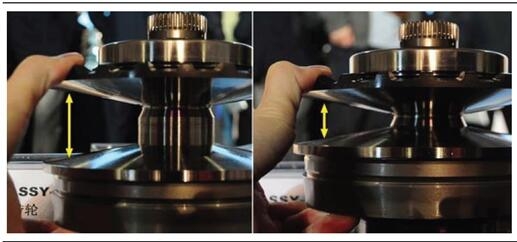
资料来源:公开资料整理
金属带-锥形轮是一种摩擦传动装置,摩擦传动的原理即压紧不打滑,即金属带需要较大的压(张)紧力来保证动力的可靠传递,施加压紧力亦需要耗费较多能量。带-轮传动装置是通过改变带两端锥形轮的工作半径来实现传动比的改变。由于锥形轮工作半径的改变是渐进式的,因而传动比的改变也是连续的,即所谓的无级变速。但受限于所能传递的转矩,带-轮传动还必须要和液力变矩器以及齿轮传动装置串联使用,实现发动机启动以及扩大速比变化的范围。
行星齿轮系具有两个自由度,即必须固定行星齿轮、太阳轮或齿圈中一个传动元件,才能以固定速比传递动力,而固定的元件不同,其速比也不同,所以行星齿轮需要额外的离合或制动元件才能工作。其优点在于输入\输出同轴、结构紧凑、可以以较小的尺寸实现大速比传动,但需要较高的加工工艺,且额外的制动或离合元件工作需要耗费能量。行星齿轮组不仅应用于汽车变速器中,由于其2个自由度的特点,还在混合动力系统用作双动力源的耦合装置。
定轴齿轮系在机械传动中使用最为广泛,是各种机械传动装置中效率最高的,其缺点主要是尺寸较大。
行星齿轮系组件示意图
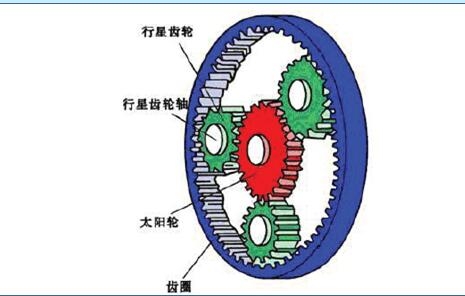
定轴齿轮及齿轮轴

自动变速器中主要传动部件的特点对比
传动部件
|
传动方式
|
优点
|
缺点
|
应用类型
|
液力变矩器
|
液力传导
|
能够吸收振动和冲击
|
效率低、质量大
|
AT、CVT
|
金属带-锥形轮
|
摩擦传动(压紧不打滑)
|
速比连续变化
|
效率低传递转矩受限
|
CVT
|
行星齿轮
|
齿轮啮合(2自由度)
|
同轴传动结构紧凑
|
工艺要求高需额外控制元件
|
AT、CVT
|
定轴齿轮
|
齿轮外啮合(1自由度)
|
效率高
|
尺寸大
|
AMT、DCT
|
以对自动变速器中各主要传动部件特点的分析和对比为基础,可以对4 种自动变速器的性能及其未来的发展方向进行总结:
AT 的传动部件一般包括液力变矩器和行星齿轮组。AT 换挡品质好,适用于各种功率范围的乘用车和商用车,但结构复杂,控制精度要求高,成本高、重量大、传动效率低,是目前应用比例最高的自动变速器,未来的发展方向是进一步提高传动效率并简化结构和控制,减轻质量。
CVT 的传动部件一般包括液力变矩器、行星齿轮组和金属带-锥形轮组件。换挡舒适性好是CVT 的主要优点,但转矩容量小限制了适用范围,液压部件造成了传动效率较低,目前在日系车中应用较多,未来的发展方向主要是扩大转矩容量和提高传动效率。
AMT 采用同步器换挡,同步器通过机械结构实现挂入挡位的转速同步,其工作的前提是主动部分的转动惯量足够小,所以AMT 换挡时离合器必须分离。离合器分离造成动力中断,所以AMT 的换挡品质较差。AMT 虽然适用于任何功率范围的车辆,但相对较差的舒适性限制了应用比例。未来的发展方向主要是避免或缓解换挡动力中断,以提升换挡舒适性。
WDCT 和DDCT 通过下一挡位同步器的预先结合,两离合器搭接控制的方式实现挡位切换,既克服了AMT 换挡动力中断的缺点,又实现了较高的传动效率。WDCT 的液压组件需要耗费较多能量,降低了传动效率,且增加了质量和成本,但扭矩容量更大,适用范围更广。DDCT 采用干式离合器,结构简单、体积小、质量轻,但热容量有限,承载扭矩范围小。总体来看,WDCT 的应用比例将会进一步提高。DCT 的可靠性和适应性仍需进一步提高,适用范围将会进一步扩大。
各种自动变速器的性能对比
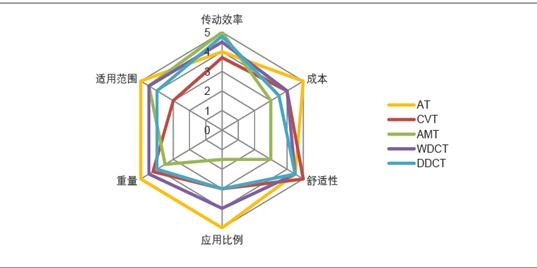
各种自动变速器的发展和提升方向
类型
|
发展和提升的方向
|
发展和提升空间
|
AT
|
提高传动效率,简化结构和控制、减轻质量
|
★
|
CVT
|
提升扭矩容量,提高传动效率
|
★★
|
AMT
|
克服换挡动力中断,提升换挡品质
|
★★★
|
DCT
|
提高产品稳定性,扩大适用范围
|
★★★★
|
4、各种类型自动变速器的搭载情况
对世界主要汽车品牌的自动变速器搭载情况进行了统计,从搭载的品牌数量来看,AT 仍是当今世界的主流,特别在北美地区占据绝对的统治地位;DCT 已在欧洲占有领先优势,并正在快速发展;CVT 主要在日系品牌中得到应用;AMT 在乘用车中应用较少。
世界主要汽车品牌的自动变速器搭载情况
类型
|
搭载品牌
|
AT
|
通用 福特 克莱斯勒 丰田 本田 三菱 现代 标致 大众 雪铁龙 宝马 奔驰
|
CVT
|
日产 丰田 本田 奥迪 克莱斯勒
|
AMT
|
菲亚特
|
DCT
|
大众 奥迪 福特 菲亚特 沃尔沃 保时捷 宝马 奔驰 三菱
|
资料来源:公司公告
目前世界自动变速器的产业格局是各国汽车产业长期发展的结果。
2009-2014年中国汽车自动变速器供求平衡统计(万台)
年份
|
产量
|
进口
|
出口
|
需求量
|
2009年
|
222.3
|
207.4
|
13.8
|
415.9
|
2010年
|
294.8
|
277.6
|
58.6
|
513.8
|
2011年
|
311.6
|
311.7
|
8.7
|
614.6
|
2012年
|
373.4
|
306.5
|
20.5
|
659.4
|
2013年
|
379.1
|
507.8
|
49.2
|
837.7
|
2014年
|
400.5
|
531.4
|
54.7
|
877.2
|
资料来源:中国海关
2009-2014年中国汽车手动变速器供求平衡统计(万台)
年份
|
产量
|
进口
|
出口
|
需求量
|
2009年
|
1162.7
|
79.6
|
36.3
|
1206
|
2010年
|
1537.2
|
127.4
|
55.7
|
1608.9
|
2011年
|
1543.4
|
132.2
|
102.7
|
1572.9
|
2012年
|
1564.6
|
122.5
|
100.6
|
1586.5
|
2013年
|
1849.9
|
141.3
|
169.4
|
1821.8
|
2014年
|
1952.2
|
135.5
|
182.5
|
1905.2
|
资料来源:中国海关
产业信息网发布的《2015-2022年中国汽车变速器行业全景调研及投资战略咨询报告》显示,2012年我国汽车自动变速器需求市场规模为717.2亿元,2013年行业规模增长至734.6亿元,较2012年同期增长2.4%。当中国内进口产品金额达到50.8亿美元。2014年我国汽车自动变速器需求市场规模增长至820.8亿元。
2009-2014年我国汽车自动变速器市场规模走势图
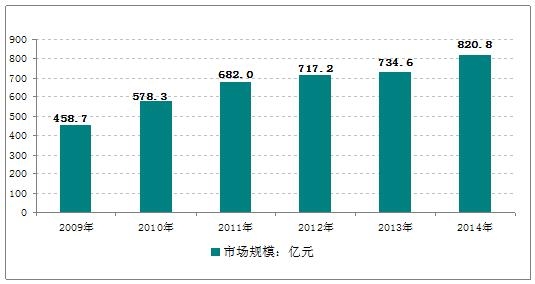
资料来源:智研数据中心整理
我国生产的汽车以配套安装液压助力循环球转向器及液压助力齿轮齿条转向器为主。目前国内市场上有140 余家转向系统零部件生产厂商,专业生产转向器的厂商有30 余家,年产量达20 万台以上的厂商有10 余家。目前我国转向行业企业生产的产品种类齐全,已形成一定规模并达到较高水平,并向经济规模型、科技创新型方向迈进。根据汽车工业协会统计, 2014年末,我国汽车转向行业产能约为3600 万台(套),总销售额约350 亿元。
2010-2014中国汽车转向行业产量(万套)
年份
|
产量
|
2010
|
1882
|
2011
|
2258
|
2012
|
2600
|
2013
|
3000
|
2014
|
3325
|
资料来源:智研数据中心整理
我国汽车转向行业发展现状如下:
(1)自主品牌厂商逐渐壮大
随着我国自主品牌汽车的发展,汽车转向行业自主品牌厂商逐渐壮大。根据《汽车转向行业“十二五”发展规划》(草案)统计的数据,目前中国生产的商用车约85%配装自主品牌转向器,乘用车约50%配装自主品牌转向器。部分实力较强的自主品牌厂商已经成功进入外资品牌整车配套市场,并实现替代。我国自主品牌转向系统零部件生产厂商已经具备与外资品牌厂商竞争的实力。
2)主流产品技术成熟
我国自主品牌转向系统零部件生产厂商的自主开发能力逐步提高,基本具备了商用车及经济型轿车转向系统零部件配套开发能力。主流产品机械和液压助力循环球转向器、机械和液压助力齿轮齿条转向器的制造技术已比较成熟。但在高端技术研发方面与国外知名厂商相比,尚存在一定差距。
(3)转向系统零部件出口规模日趋扩大
近年来,欧美及日本厂商加大了在我国的投资力度,建立生产工厂。而我国主要汽车零部件厂商也出国收购外国厂商汽车零部件业务资产,例如2010 年北京太平洋世纪汽车系统有限公司成功收购通用旗下NEXTEER 汽车转向与传动系统业务。随着国际汽车零部件生产重心向我国及东南亚国家转移,我国汽车零部件行业出口规模增长迅速。
资料来源:公开资料整理